Pulling Out All the Stops
Evolving coatings and finishes for automotive brake components.
Edited by Scott Francis
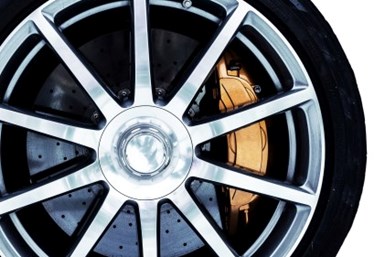
Brakes
Photo Credit: All images courtesy of MacDermid Enthone
Making a vehicle go is important. But, making it stop is critical and surface finishing plays an important role in making sure brake systems perform effectively and withstand the elements and harsh conditions that the road and the weather expose them to. Products Finishing recently sat down with Rene van Schaik, global strategic accounts director, MacDermid Enthone Industrial Solutions, to hear his insights into the many important ways that surface finishing protects and enables automotive brake systems.
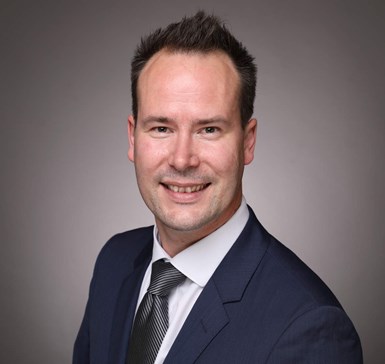
Rene van Schaik, global strategic accounts director, MacDermid Enthone Industrial Solutions
PF: Can you talk a bit about the various chemistries involved in coating brake system components?
RS: It’s important to understand that there are different types of brake systems used, depending on the class of vehicle. There are floating brake caliper systems, fixed brake caliper systems, and drum brakes. Drum brakes are typically for lower end vehicles, though we see them growing in use for electrical vehicles. Fixed brake calipers are relatively expensive — but they’re the best ones there are — they have large aluminum calipers. And then there are floating brake systems with floating calipers, these can be either cast iron, or cast iron aluminium mixtures.
For aluminum components, anodizing products and conversion coatings are used to help adhere certain paints or lacquers. For the cast iron caliper components, there are different zinc plating systems or zinc alloy plating systems.
But, when you look at the brakes as a whole, it’s more than the calipers. There are caliper housings and brackets, and there are also bolts and pins that go into the brake system. There are pistons, brake pads, tubes and fittings — all of which require coatings. So, for example, on fasteners, it would be an alkaline zinc or an alkaline zinc nickel. On calipers, it would be acid zinc or acid zinc nickel, because the acid systems have different plating characteristics than the alkaline ones. The plating initiation is a lot faster, which is needed for these cast iron materials. Pistons, for example, would require hard chrome or electroless nickel.
PF: I'm sure you also have to consider how the coatings on different parts interact with each other, correct?
RS: That’s really important, yes, as they’re connected to each other. So, there’s a very strong trend, for example, to zinc nickel as opposed to pure zinc. And a lot of that has to do with increased use of aluminum for lightweighting for electrical vehicles or improving fuel economy. It takes certain coatings that can work in combination with aluminum. Zinc nickel is a very good one that’s compatible with aluminum.
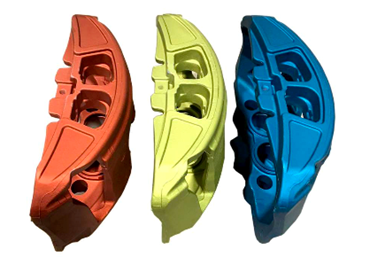
Brakes
PF: When it comes to brakes, reliability is paramount. Can you talk about the role coatings play in terms of corrosion and wear resistance?
RS: Obviously, safety is a very big requirement. Corrosion protection is a key factor, as you mentioned, and wear resistance as well. Brake fluid compatibility is another consideration. If the incorrect coating is applied, it might dissolve when in contact with these brake fluids. So, that's why we use inorganic sealants typically as opposed to organic sealants.
Coating adherence toward a paint or a powder coating also needs to be considered. This contributes to wear resistance to stone chipping, for example. In addition, as the brakes push into the disk, there’s a lot of heat generated. So, resistance to temperatures is also required. In addition, you need to consider UV resistance and weathering fastness.
Finally, don’t forget the appearance. Since most of the designs today are open wheel designs, you can actually see the brakes. Especially with luxury vehicles, people are showing off their brake systems. Sometimes you see colorful brakes — bright green, gold, black, blues. Or they need to be uniform silver. Back in the 80s, even the most iconic cars had closed wheel designs, but today with more open wheel designs, the appearance of the brakes has become quite important.
PF: The final finish isn’t the only chemistry involved — can you talk a bit about the importance of pre-treatment in finishing brake systems?
RS: Everything starts with pretreatment, and that’s even more valid for cast iron or cast aluminum materials compared to steel or standard aluminum components. That’s because these casting materials have certain roughness or holes in them that needs to be pretreated in a specific way to ensure that you can have a uniform good finish after plating.
The pretreating sequence is important. For cast iron caliper components, it’s very important to have an ultrasonic positioned after the pickling, to get rid of any contamination or filth that might be entrapped in these holes of the cast iron. These absolutely have to be removed from these cavities prior to the plating process. Otherwise, they get trapped underneath the plating layer and then you get all sorts of delayed defects afterwards.
The same is valid for cast aluminum. The pretreatment is necessary for the anodizing process to be efficient. If the layer is not smooth, then the anodizing layer can’t build in a sophisticated way, and then it will be non-uniform and the appearance won’t be very nice.
Unfortunately, what we’ve seen since the start of the pandemic, and during the supply chain interruptions, is that the casting quality has gone down in recent years. But, even with more challenging casting qualities, our products need to provide a consistent quality and help our customers meet certain first pass yield standards. So, it’s increasingly important, from that point of view, that we also help advise the customers on the pretreatment line design and layout, and also, in certain cases, provide auxiliary equipment that can provide quality, sustainability or economic advantages for customers.
PF: How have brake systems evolved in recent years? Are emerging applications like electric vehicles, hybrids, and new energy vehicles changing the way we think about brakes? If so, what does that mean for the surface finishing solutions involved?
RS: The automotive industry is evolving and there are a lot of new trends coming. While some of these trends have been around for many years, the world wasn’t ready for them. But today, in some regions more than others, you can see that it’s really pushing through. In Europe and Asia, there are a lot of electrical vehicles already on the road. In some parts of Europe, 50% of the cars on the road today are already electrical. In the future, there will be even more changes such as hydrogen systems.
As I mentioned before with brakes, we have to distinguish between low end, mid class and high end vehicles. I think that still applies whether it’s an electrical vehicle or not. And the other thing that we should bear in mind is that there’s a difference between the brake systems between the rear axle usage and front axle usage. So, in today’s combustion engine, there’s a difference between front and rear. And in the electrical vehicles, we also see it as a difference.
When we really look at the brake systems, I talked about the fixed calipers and the floating brake calipers and the drum brakes — will those significantly change? No, that’s not something we should expect to see in the short term.
For floating brake calipers, a trend that we do observe in light of light weighting is that maybe the bracket is made of cast iron and then it’s combined with an aluminum housing. And of course, zinc nickel is important as I mentioned earlier, to avoid contact corrosion.
You also see regenerative braking used on new cars, meaning brakes are used less and therefore the corrosion resistance has to be even higher and longer. So again, that is the explanation why it would go to zinc nickel as opposed to zinc.
So one of the trends that we observe with electrical vehicles is that drum brakes are rising in popularity a little bit again. While drum brakes were typically only used in low end vehicles for a long time, we are now are seeing mid class electrical vehicles are equipped with drum brakes in the rear axle usage. And as part of that, we’re seeing more closed wheel designs or semi closed wheel designs again. That’s partially to improve the aerodynamics for the driving distance of course, but also to make the use of drum brakes less visible.
Other new designs include wheel hem consisting of an inner aluminum carrier and an aluminum brake disc. This avoids flash rust on the disk and also reduces noise. Because electric vehicle engines are very quiet, there’s a high focus on the brake systems to have no sound at all.
The other trend we haven’t even spoken about is autonomous driving. For fully autonomous driving, the brake systems can work with very small calipers that can be fully integrated inside of the wheel. Because the emotions are eliminated, there’s no speeding, there’s no emergency braking.
PF: As these trends continue to evolve, all that R&D work continues, right?
RS: Absolutely. That’s why our company is very much involved, not only with at applicator level and the tier ones, but also at the OEM level. We want to know where these trends are going because products are not developed from one day to the next. Sometimes they take years. We need to know early in the game where it’s going and what we need to develop to help the industry to give the new materials the right characteristics to ensure safe performance.
RELATED CONTENT
-
Efficiently Painting Bytons
A paint shop being built by Dürr Group in Nanjing for the Future Mobility Corp. is being setup for an initial run of 150,000 vehicles per year (30 per hour) and for the potential of doubling that number.
-
7 Cool Tools: Laser Cutting, Fixture Modeling, and more
Increase operational productivity with these new developments for automotive manufacturing from Mazak, Renishaw, Omron, Marposs and more.
-
on Painting Porsches, Running Trains on Hydrogen & a New ICE from Stellantis
Painting 911s, running trains with hydrogen, charging with a quantum approach, and developing a new engine at Stellantis