Robots, AI and Superb BMW Surfaces
There isn’t an automotive paint shop in the world that doesn’t have post-paint inspection and defect processing. But BMW is doing this with levels of technology at a plant in Germany that exceed all other paint shops in the world.
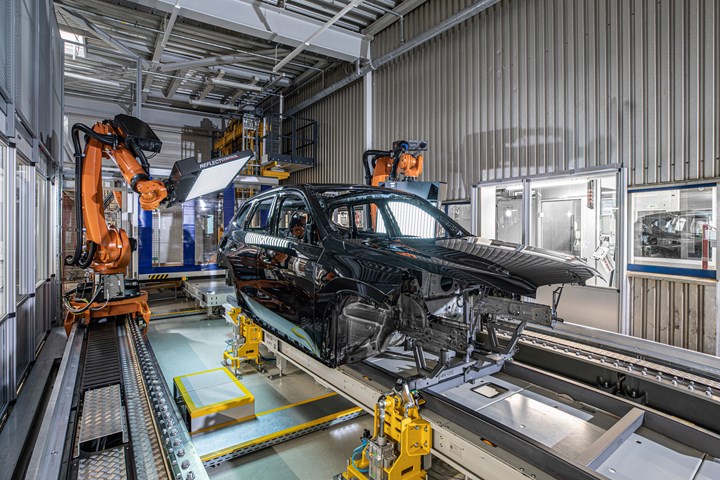
Deflectometry is used to detect any defects on the painted surfaces of the BMW 1 Series, X1 and X2 models produced at the company’s plant in Regensburg, Germany.
Photo Credit: All photos courtesy of BMW
Everyone is talking about AI. BMW is doing something about it — or more specifically, with it, as it is deploying AI to achieve superb surfaces on the 1 Series, X1 and X2 models that it is producing at Plant Regensburg in Germany.
As is common in automotive paint shops, after the topcoat is applied, surface inspection is conducted. Here they are using deflectometry to assess the surface. Black and white striped patterns are projected on the vehicle and then cameras are used to scan and detect any flaws on the reflective paintwork. Simply: if there is a defect, it affects the striped pattern.
While using deflectometry is typical in automotive paint facilities, what’s not always the case is that the BMW system cameras register the locations of the defects and the data is uploaded to a computer system. Then a digital 3D image of the deviation is created, classified and stored. Each scanned body — and they are producing up to 1,000 vehicles per day in the factory — has its own profile created; that is then used for the subsequent surface processing. The data is stored in the cloud.
Ordinarily, this scanning involves highly trained human operators. BMW’s Daniel Poggensee, a structural planner for Surface Technology, says, “The system already knows as much today as our best employees combined. We used the knowledge of our entire team to finalize the system; the functioning of the equipment relies on our associates’ unique expertise. We channeled their experience into the programming — on this basis, the algorithm now recognizes and objectively decides which features need post-processing.”
What’s more, the system determines the optimal order in which the surface flaws are addressed by an AI-based, automated surface processing system.
So there is a given body. The scanned and processed data is delivered to a processing booth where there are four robots. Here the problem areas are being sanded, having polishing compound applied, and being polished. Attachments and sandpaper are automatically swapped out.
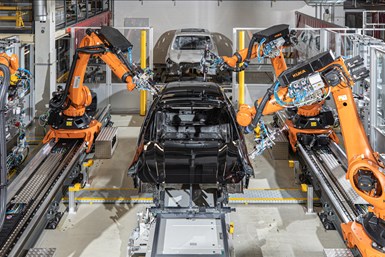
Vehicles move into a booth where robots remove the defects from the surface. The locations of the defects and the order in which they are addressed are based on an AI assessment.
Work Where It Is Needed
Here’s the notable aspect of the operation, which BMW says is the first end-to-end digitized and automated process for inspecting, processing and marking painted vehicle surfaces in serial production:
Stefan Auflitsch, head of Production Paint Application and Finish at BMW Group Plant Regensburg, explains, “What is unique here is that the robots work on each body exactly where needed — because the tiny specks and bumps that can appear after the topcoat is applied and that we want to remove are in different spots on each vehicle.
“Robots are normally programmed to follow the same pattern until they are reprogrammed. Using artificial intelligence allows them to work in a more tailored manner. With up to 1,000 vehicles going through the finishing process every working day, that adds up to 1,000 unique processes.”
Consider: Whereas conventionally controlled robots are highly deterministic in terms of following a set pattern — A to B to C to D to E — the AI-controlled robots are going to the places on the painted body where the defects need to be addressed and in the most efficient order — B to D to A to E, possibly not needing to go to C for a given vehicle, or to any other location as required (F, G, H, etc.).
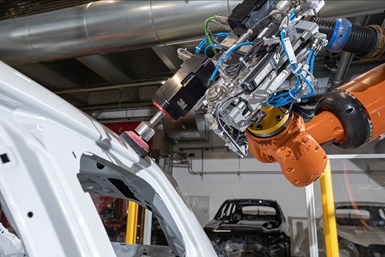
The robots change their end effectors as needed for sanding and polishing the surfaces.
Still a Human Touch
All of that notwithstanding, people are brought into the process at Plant Regensburg, too.
Turns out that the robots aren’t good at dealing with the edges of the vehicle body nor close up to joints, such as at the doors. Also, the fuel filler cap is too fragile for robot processing.
So BMW associates are used to address problem areas. But even here, advanced tech is used to ensure that all defects are addressed: a laser projector is used to “mark” the issues on the sheet metal so the workers know where to go.
Poggensee thinks the data being accumulated in the cloud might allow them to determine whether there are process inconsistencies such that it “will enable us to prevent faults from occurring in the first place.”
And that would be the best-painted surface of all.
RELATED CONTENT
-
GM Seeks to Avert U.S. Plant Shutdowns Linked to Supplier Bankruptcy
General Motors Co. says it hopes to claim equipment and inventory from a bankrupt interior trim supplier to avoid being forced to idle all 19 of its U.S. assembly plants.
-
When Automated Production Turning is the Low-Cost Option
For the right parts, or families of parts, an automated CNC turning cell is simply the least expensive way to produce high-quality parts. Here’s why.
-
On Electric Pickups, Flying Taxis, and Auto Industry Transformation
Ford goes for vertical integration, DENSO and Honeywell take to the skies, how suppliers feel about their customers, how vehicle customers feel about shopping, and insights from a software exec