On Audi and Volvo's Green Initiatives, Bentley Design and more
Audi takes to the river to reduce plastic waste, Volvo focuses on a new category of consumers, Bentley once used a Bob Ross-approach during styling development, why Ford’s BlueOval City is the past brought to today, and some new terms that you should keep in mind
#robotics
This week On Automotive
- Audi on the Danube
- Term to Know: “Regenizens”
- Bentley Marks 70 Years of In-House Design
- British Car, Slovenian Exhaust
- Term to Know: “Reservoir Computing”
- Enter the Droids
- Ford Back to Its Roots
///
Audi on the Danube
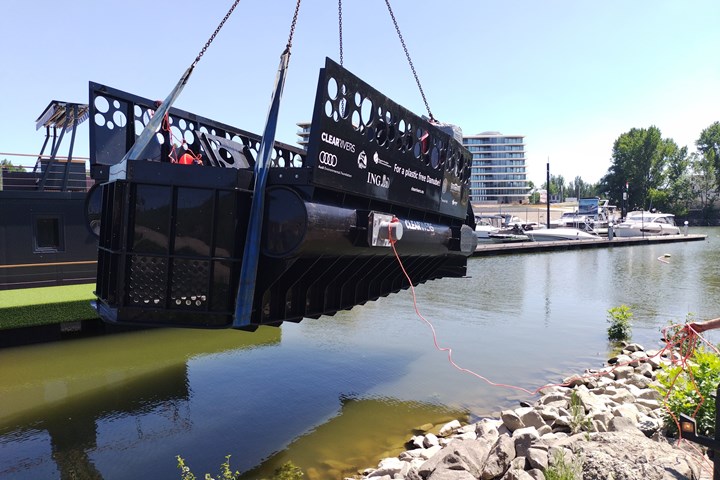
An Audi development you can’t drive: This collects plastic waste on rivers. (Image: Audi)
Clearly, that object above is not an Audi. At least not as we know them.
But it is from Audi. Audi Hungaria. And the body of water it is in is the Danube.
(Doesn’t look particularly blue, does it?)
The object is a mobile plastic catch basin. It is going to be attached to an existing floating pontoon and installed in front of the Budapest University of Technology and Economic.
Here’s the clever bit:
The trap is a passive system that will collect floating plastic waste, with the design of the partition panels being such that it doesn’t interfere with fish or other denizens of the Danube.
They can swim under it.
Audi’s position
Rüdiger Recknagel, Managing Director of the Audi Environmental Foundation:
“Following the successful installation of previous plastic traps in Rotterdam and the Charleroi canal in Brussels, the litter trap in the Danube in Budapest now adds a further European site where we are actively working against water pollution. More than 90 percent of the plastic in the oceans is transported there via rivers. Avoiding plastic waste in the environment is therefore one of the central aims of our foundation’s work.”
Plastics that have been collected so far have been turned into benches that are installed at several Audi production facilities.
Audi has been working with the CLEAR RIVERS organization on dealing with plastic waste in waters since 2018.
///
Term to Know: “Regenizens”
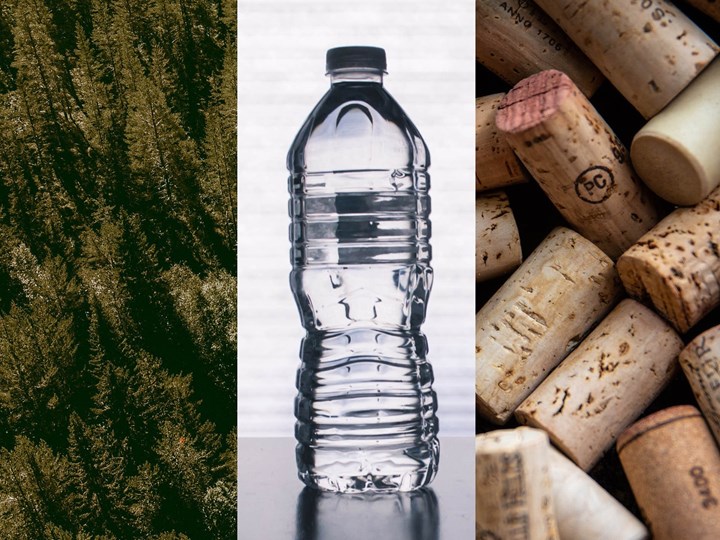
Volvo is finding materials like these—yes, even used wine corks—provide the means to make components for vehicles, which is something that a growing set of consumers feel good about buying. (Image: Volvo)
Linn Fortgens, head of sustainability procurement at Volvo Cars:
“The external awareness around the fundamentals behind sustainability – not just aspects like understanding carbon footprints – but fully sustainable products, including things like circularity and responsible sourcing, has grown tremendously over the past couple of years.
“Now, we really see it playing out in consumers’ choices.”
Those consumers are “Regenizens.”
Huh?
According to report produced by Volvo with trend forecasting company The Future Laboratory, they are “community-focused citizens reframing their relationship with consumption to be not just more sustainable, but also regenerative and ethical.”
This approach, the report says, has been “accelerated by the pandemic, with events of the past year reminding us how interconnected we remain in a globalized world.”
Volvo is making efforts to address the interests of these people (the OEM cites a Capgemini study that shows 79% of consumers changing their “purchase preferences based on social responsibility, inclusiveness or environmental impact,” so its not like this is an ignorable cohort):
- It has announced all of the vehicles it builds will be fully electric by 2030
- It plans for 25% of the material being used in new vehicles being recycled or bio-based, with a goal of being a fully circular business by 2040
- It is working to eliminate use of leather in interiors, with alternatives such as “Nordico,” a material it developed based on textiles made from recycled material such as PET bottles, bio-attributed material from sustainable forests in Sweden and Finland, and corks recycled from the wine industry.
Robin Page, head of design at Volvo Cars:
“We have a vision of where we need to go in the future, with the first step to ensure we harness sustainable, natural and recycled materials. The next challenge is to change what we do with these materials, whether that’s making car parts that last forever, re-enter the circular economy or go back into the earth.”
An approach that will undoubtedly be appealing to Regenizens.
///
Bentley Marks 70 Years of In-House Design
The first in-house design of a Bentley occurred in 1951. It was the R-Type Continental.
Back in 1951 when the company established its design department at its HQ in Crewe, the designers shared their concepts with colleagues in other parts of the business with. . .hand-painted watercolor renderings.
Yes, sort of like Bob Ross.
Designs given a green light then became full-size technical drawings: side, front, rear, plan and sectional views.
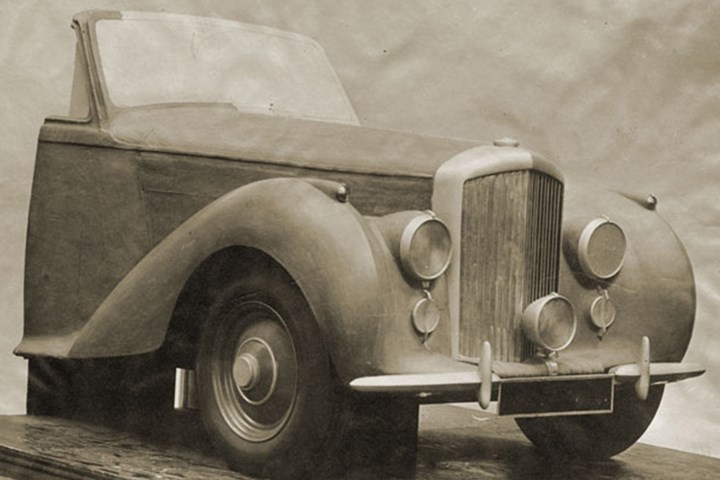
Bentley modeling back in the proverbial day. (Image: Bentley)
The physical 3D models of the 1950s sculpted in Crewe were not entirely different than those produced today.
A metal framework was covered with a malleable material.
While the material of choice today is clay, back in the early days at Bentley the modelers used wax.
///
British Car, Slovenian Exhaust
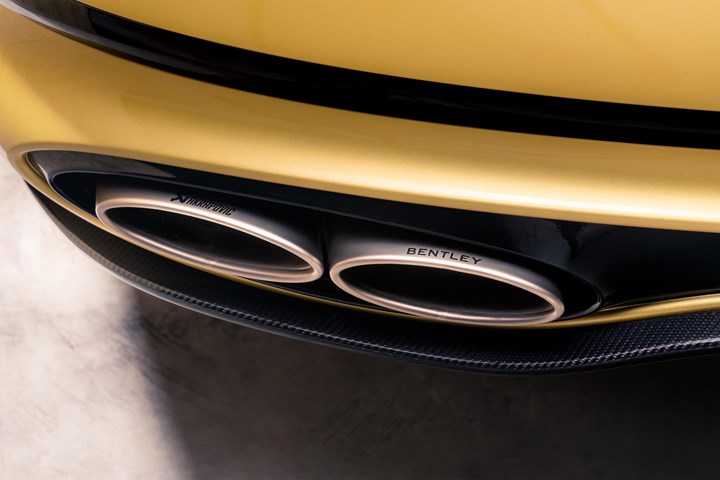
Specialized exhaust for Bentley: fabricated with titanium. (Image: Bentley)
One more thing about Bentley and materials.
Not wax or clay.
Titanium.
(And some superalloys, to boot.)
Bentley is offering lightweight sport exhaust systems for the new Continental GT Speed and GT Speed Convertible that is being produced by Akrapovič.
Who?
A Slovenian manufacturer of premium exhaust systems that was established in 1990 by Igor Akrapovič to produce exhausts for performance motorcycles; he held several motorbike championships, so it was something he had well-earned knowledge of.
Racing—incidentally—was involved in the development of the exhaust for the new Bentleys: the run in the 2019 Pikes Peak International Hill Climb, when a Continental took the Production Car record, with Rhys Millen piloting the car up the climb in 10 m 18.4 s, besting the previous record by 8.4 seconds.
The engine that it is fitted to is a turbocharged 6.0-liter, 641-hp, W12.
Among the benefits of the exhaust is improved throttle response because there is lower system back pressure, which improves turbocharger performance.
And it reduces the weight of the vehicle by 7 kg.
(With a curb weight of 2,244 kg, it might not be that noticeable. But every gram matters.)
///
Term to Know: “Reservoir Computing”
In a nutshell, this is a machine learning algorithm that can solve complex problems (1) fast and (2) without the need for massive hardware.
While it has been around for the past few years, researchers at The Ohio State University have developed a new approach to reservoir computing. For example, mathematicians looked at the neural networks closely to determine what is required and what isn’t, and so simplified the system. And while there has been a need to load as many as 10,000 data points simply to train, or “warmup” the system, the new approach may need just three data points.
The thing is, reservoir computing is mainly focused on solving problems associated with dynamic systems. Like the weather.
What about auto?
But we wondered about any automotive applications—like computational fluid dynamics.
We asked Dr. Daniel Gauthier, who is working on the new approach with colleagues at OSU. (And a professor of physics there.)
So. . .?
“I believe so. We are starting to work on more complex problems involving spatial dynamics that you would encounter in fluid dynamics problems. However, there is already previous research on this topic using traditional reservoir computers and it works great. So I believe that our reformulated algorithm should just speed up the process and make the resulting artificial neural network more interpretable. For a large spatial-temporal system, will need more computational resources, but likely much less than you would need for the full physics-based simulation. The idea is that you can infer data at other spatial locations using the artificial neural network and this is likely to speed up the simulations.”
He adds, “You can also use it based on data assimilation. You can also make a hybrid system where the artificial neural network takes as input data from an physics-based simulation, experimental data, and then makes a prediction that is often better than the simulation.”
This is fast
When he mentions “speed up” know that when running a weather system forecasting task (the Edward Lorenz “butterfly effect”), the new reservoir computing system ran it 33 to 163 times faster than the current model. And they did it on a laptop.
Know that the computer hardware is modest.
Gauthier says at his company ResCon Technologies they’ve developed an adaptive autopilot system for drone that uses the flight computer found on smaller drones. Not a whole lot of hardware.
///
Enter the Droids
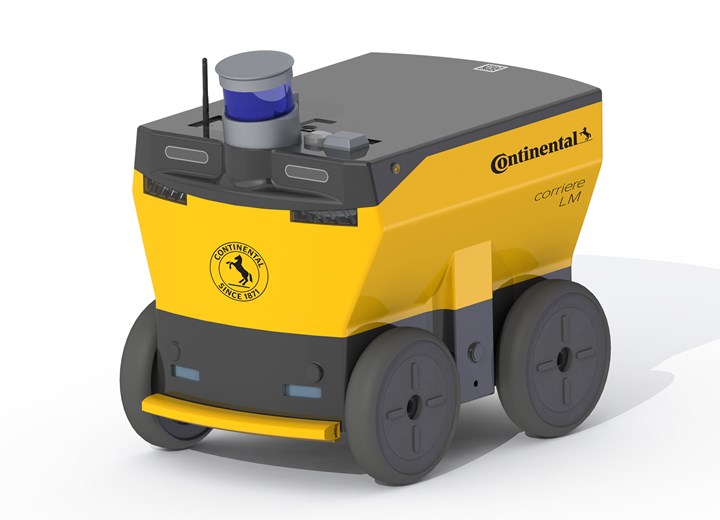
This little droid—about a foot high—is currently making lunch deliveries to Continental workers in Singapore. (Image: Continental)
"Innovative mobility also means meeting the challenges of higher logistics volumes, implementing sustainable ideas for the transport and distribution of goods, and offering smart solutions that support resource-efficient food production in agriculture. For all these areas, robotics applications are an ideal complement to existing structures."
That’s Michael Hülsewies, Senior Vice President and Head of Architecture & Software at Continental.
Continental as in the automotive supplier.
The company has developed three AMRs—Autonomous Mobile Robots.
- Corriere. A small (about a foot high) urban delivery robot. It is fitted with lidar and camera sensors. It has self-learning software. It can recognize pedestrians and cross streets. Conti is testing the Corriere in Singapore, where it is used to deliver food from a restaurant to the company’s local site.
- Contadino. This is engineered for agricultural applications. It weighs about 220 pounds, and can carry about 310 pounds—things like seeding, planting or fertilizing modules. The comparative light weight is said to be good to keep the ground from being compacted. Thanks to a satellite communication system and weather apps, the Contadino can target a plant within 1.2 inches. That means it can, say, individually fertilize plants.
- Unnamed. This is simply referred to as an “autonomous intralogistics robot.” It is a material handling device that is presently carrying heavy components at Conti plants in Slovakia and China. The company couldn’t find an existing product that met its requirements so they built one. It is equipped with lidar and cameras. It can be fitted with an ultra-wideband transmitter for precise tracking.
Not all autonomous vehicles are things on highways.
Some for sidewalks. Some for fields. Some for factories.
///
Ford Back to Its Roots
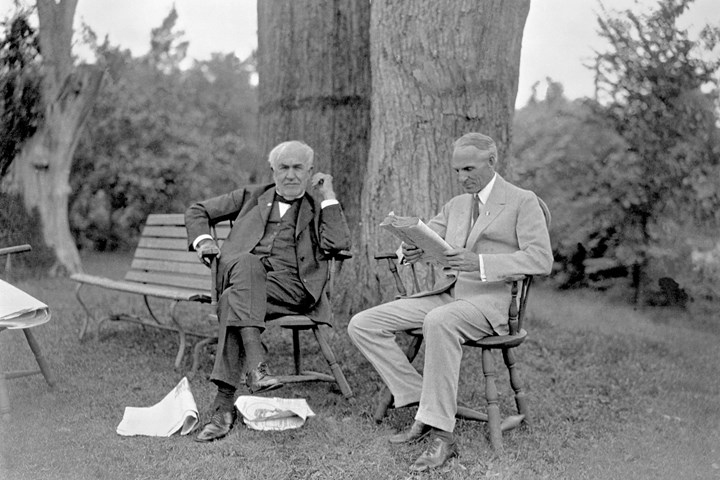
Thomas Edison and Henry Ford: These guys both had it right. (Image: Ford)
Henry Ford and Thomas Edison were pals. Not surprisingly, Edison was a proponent of electric vehicles. Henry actually worked on the development of an EV in the mid-teens of the 20th century.
Reports on why this didn’t happen are varied, with some suggesting that Edison wanted the vehicle to be powered by the nickel-iron battery he’d developed but they made the vehicle not as functional as it would need to be for a practical man like Henry. (Remember: the Model T has so many uses that it was a veritable Swiss Army knife on wheels.)
And now. . .
The $11.4-billion that Ford and South Korean tech company SK Innovation have announced will be invested in a vehicle assembly plant for “an expanded lineup of electric F-Series vehicles”—which seems to imply there are a lot more coming than just the forthcoming Lightning—as well as three battery plants (one in Kentucky at the assembly complex, which is being called “Blue Oval City,” as it measures nearly six square miles in footprint; two in central Kentucky, the “BlueOvalSK Battery Park”) is a lot of money. Blue Oval City accounts for $5.6-billion and BlueOvalSK Battery Park accounts for the remaining $5.8-billion.
Of the money, Ford is spending $7-billion.
This is said, by Ford, to be the biggest manufacturing investment made by an automotive manufacturer in the U.S. at one time.
Last May Ford announced that it would be spending $30-billion on EVs through 2025, so at some point something like this was probably inevitable.
The historic redux
Here’s an interesting aspect to all of this.
Ignore for a moment the fact that the topic is electric vehicles and batteries.
What Ford is doing at Blue Oval City is what Henry did at the Rouge Plant in Michigan. The Rouge, which opened in 1918, became an increasingly vertically integrated manufacturing operation. They were shipping in iron ore and making steel; they were bringing in logs that had been cut down in northern Michigan and using them to produce components for the Model T. And so on.
After years of spinning off things that were not seen to be core, there is now an evident recognition that it is good to have the wherewithal to control operations.
The return to vertical integration is as important as the scale of the investment.
RELATED CONTENT
-
TRW Multi-Axis Acceleration Sensors Developed
Admittedly, this appears to be nothing more than a plastic molded part with an inserted bolt-shaped metal component.
-
Revolutionary Hydrogen Storage Tank Design Could Propel H2 Deployment
Rather than storing hydrogen in a large cylindrical tank, Noble Gas has developed a conformal system
-
On EV Sedans, Self-Driving Tech, 15-minute Cities and more
Will EVs save the sedan? Will anyone in the UK tell grandpa to give up the keys? What to do with broken windshields. And much more.