On Audi's Paint Colors, the Lexus ES 250, and a Lambo Tractor
From pitching a startup idea to BMW to how ZF is developing and using ADAS tech to a review of the Lexus ES 250 AWD to special info about additive at Toyota R&D. And lots in between.
This week On Automotive
- BMW and the Art of the Pitch
- Color Me Jealous: Audi Sport
- How to Pack a Chiron
- From Small Seeds. . . The first Lamborghini isn’t what you may think
- How ADAS Gets Done
- Well, It Snows A Lot in Sweden: Autonomous vehicle testing moves indoors.
- 2021 Lexus ES AWD F-Sport
- Additive @ Toyota Motor North America R&D
///
BMW and the Art of the Pitch

Inside the BMW Startup Garage (Image: BMW)
The “elevator pitch” is something that is historically non-automotive.
OEMs tend to prefer working with well established companies that are as old as they are.
The start-up culture has long been. . .well, not what you necessarily want to depend on when you’re producing millions of vehicles.
That said, things are changing.
Start me up.
“We have believed for a long time that startups have a key role to play in helping us shape individual, connected and sustainable mobility.”
So says Bernhard Schambeck, head of BMW Startup Garage.
That “long time” may be a bit of an exaggeration. BMW established its Startup Garage in 2015.
Still. . . .
BMW has announced the Open Call 360° Startup Challenge.
The winners—those that have something that BMW reckons will have an effect on its sustainability efforts—will gain access to the BMW Startup Garage venture client program. Which could mean almost-instant scale. And funding.
Categorically.
Here are the categories in the Open Call 360° Startup Challenge:
- Recyclable materials
- Sustainable supply chain
- Energy-efficient production
- Mobile intelligence
- Intelligent building management
- Customer-centric mobility
- Sustainable technologies
Perhaps the sort of thing your company should be getting pitches about.
If you want to sign up this is what you need to click.
///
Color Me Jealous

Six colorful Audis. A complete set. (Image: Audi)
Exterior colors are critically important to vehicles—and even more so to the people who own those vehicles.
So Audi Sport is offering its R8 LMS GT2 in some special colors.
It is named the “Color Edition.”
A word about the vehicle. It has a 5.2-liter, 640-hp engine built at the Audi Győr site in Hungary. The chassis is an aluminum-carbon fiber reinforced plastic structure on top of a steel roll change. The vehicle is transformed into a race car at the Böllinger Höfe in Heilbronn by Audi Sport specialists.
About those colors.
- Kyalami green
- Misano red
- Nogaro blue
- Sebring black
- Tactical green
- Vegas yellow
Six colors. And Audi is building six cars. That’s it.
Price? € 349,000 (plus VAT). Which isn’t bad because a non-Color Edition model goes for € 338,000 (plus VAT).
(Six cars!)
///
How to Pack a Chiron

Engineered to fit. (Image: Bugatti)
While on the subject of cars that go fast, when ordering your Bugatti Chiron (stated top speed for the $2,990,000 base model: 261 mph), you might want to order a set of a “Bugatti by Schedoni” luggage set.
After all, according to the OEM, the Chiron “provides its owners with accessible every-day usability and road travel.”
Certainly.
The leather luggage is a study in assembly.
By the numbers. To make a three-piece set it takes 110 hours.
There are more than 150 separate pieces of leather, 150 pieces of backing material and 50 cuts of lining.
The grade, type and color of the leather and color of the yarn can be selected from a pallet of 31 hues.
Stitching, patterns and embroidery can also be selected.
Fitted. Simone Schedoni, chairman of Modena-based Schedoni (and fourth-generation family member of the firm that’s been in the family since 1880): “Considering the amount of attention and care that goes into crafting every Bugatti model, every single piece of luggage we produce matches the same level of passion, craftsmanship and dedication. Our leather sets are especially made for the shape of the Chiron, so every item fits seamlessly, whether it is kept in the front trunk or in the cockpit.”
The luggage is part of the 3D car configurator that can be used to order a Chiron: it is that well-tailored.
///
From Small Seeds. . .

A man, his sports car and his. . .tractor. (Image: Lamborghini)
And while on the subject of cars that have a price that would skew any calculation of average transaction prices by the high number but would have little effect were the number of vehicles sold were that to be part of the figuring, know that Lamborghini is celebrating the 105th anniversary of the birth of its founder, Ferruccio Lamborghini.
What makes this all the more interesting is that vehicle on the right side of the photo above.
Yes, that is a Lamborghini tractor Ferruccio is posing with.
Turns out that tractors were the first products that the company produced when it started vehicle production. Ferruccio’s post-World War II idea was, according to the company, “to build inexpensive agricultural tractors within the reach of small landowners, using the components of old military vehicles.”
The first Lambo was a tractor that was made from a Morris truck. It was introduced in 1948.
///
How ADAS Gets Done
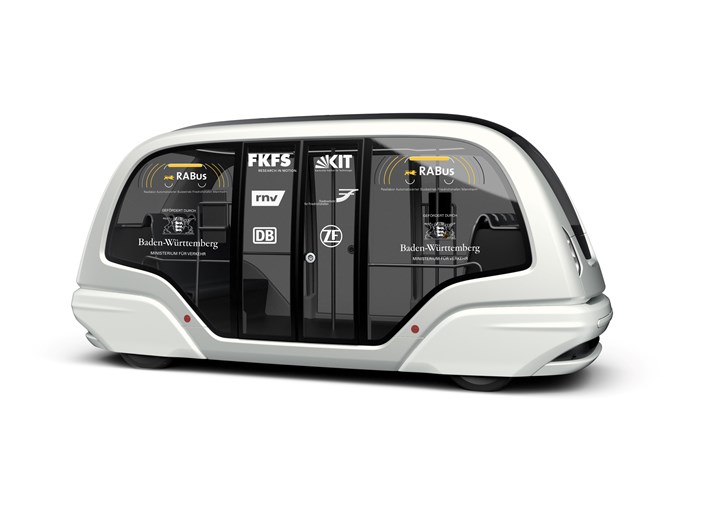
ZF doesn’t just make tech for other companies that are looking for automated driving, but it also runs its own commercial shuttle. (Image: ZF)
Although the association of ZF and things like nine-speed transmissions is well known given the company’s long history of producing leading edge gearboxes, Martin Fischer, who is president of the supplier company in North America, tells us that “what’s driving us at ZF” is. . .the development of electronics for automated driving.
“We are in a good position regarding ADAS,” Fischer says, explaining that the ZF acquisition of TRW in 2015 provided the company with a solid base in this space.
ZF, while still producing things like transmissions and steering systems, is, Fischer says, combining its mechanical and E/E competencies, which will be leading to more by-wire systems, especially with the proliferation of electric vehicles, which Fischer notes provides the electrical capacity for by-wire systems to work in ways that 12- or 48-volt setups really don’t.
Super.
At the recent Auto Shanghai ZF introduced what the company claims is “the most flexible, scalable and powerful automotive-grade supercomputer on the market.”
This is the company’s next-gen ProAI platform. Fischer notes that it can be fitted with system-on-a-chip devices from a variety of vendors, such as Qualcomm, TI and NVIDIA.
It is engineered so that it requires less power—on average three teraOPS (that’s three trillion operations per second) per Watt. There are three cooling approaches: passive, air and liquid. The form factor of the housing is the same, regardless of the processor type and cooling approach, which means better scale economies.
It can run software developed by ZF (yes, Fischer says, this is another area where ZF has gained capabilities) or third parties.
It offers the ability to run Level 2 to 5 autonomous systems, whether it is a domain, zone or central controller.
In the Space
While as a supplier ZF provides product to spec, there is also something else it is doing in the autonomous space. Something that provides it with first-hand understanding of what’s needed.
It bought a shuttle service, 2GetThere, which it is operating in commercial service in a controlled environment and which, Fischer says, it will be operating, autonomously, in “mixed traffic operations in Europe next year.”
It will be depending on its own tech to perform autonomous operations.
///
Well, It Snows A Lot in Sweden

Those vehicles aren’t tiny. That space is huge. (Image; AstraZero)
That picture above is not some sort of giant warehouse.
Although just judging from the miniscule size of the vehicles, it is giant:
2,297 feet long and 131 feet wide, with a 459-foot long width expansion to 197 feet
It is named “AstraZero.” The facility, located in Hällered, Sweden, is said to be “the world’s longest indoor autonomous vehicle test track.” Its official opening was April 28.
It is operated by RISE, the Swedish Research Institute, and Chalmers Institute of Technology. It is open 24-7.
The first commercial customer is Volvo.
Mats Moberg, Senior Vice President of R&D at Volvo Cars: “AstaZero’s facility provides a wide range of infrastructure that is important for the testing and validation of our technologies in safety, autonomous driving and connectivity, making it possible for us to perform testing in well-controlled environments all year round.”
///
2021 Lexus ES AWD F-Sport

While it has AWD, seriously: how often are your wheels really going to slip? (Image: Lexus)
It seemed somewhat ironic that even though it was late April, the day the ES AWD F-Sport showed up in my driveway snow was falling. (People in these parts say, “That’s Michigan weather: just wait a few minutes and. . . .”)
I guess that if you’re going to be driving a luxurious midsize sedan and there’s snow on the blacktop, better to have AWD than not.
More ES. The AWD was added to the ES last August. A line extension.
The vehicle is ordinarily FWD. But this system, when it detects wheel slippage as a result of snow or rain or other causes of low-μ conditions, will divert up to 50% of the available torque to the rear wheels.
Weather Stats. I’ve learned that there are 152.1 days per year when there is precipitation falling in Detroit. This leaves 212.9 days when there is nothing coming out of the sky, but there is still slipperiness on the roadways. But most days, dry.
Which, I think, is more to the point of the ES AWD F-Sport: Not slippery due to inclimate weather. Wheel slip when you mash the accelerator.
Seems odd that you would in an ES. But this would help when you want to burst off the line. To the extent you can.
What the F-Sport Adds. The “F-Sport” package means that there is a sport-tuned suspension and 19-inch wheels. There is a selector on the IP that allows the ability to select sportier modes (changes throttle response and transmission settings). There is a seven-inch cluster that provides animation and information germane to the vehicle performance. There is available “Circuit Red” color option for the interior that the non-F-Sport ES models can’t get and aluminum trim on the IP that the non-F-Sport ES models don’t get.
It is powered by a 2.5 liter, 203-hp in-line four connected to an eight-speed automatic. 203 hp is fine, but the car weighs 3,780 pounds so it isn’t exactly the sort of thing you’re going to be burning a whole lot of rubber with. And why would you?
It looks fast.
The odd thing is the ordinary FWD ES is the ES 350, which has a 3.5-liter, 302-hp V6.
Even though it snowed in April, given the nature of the ES, I’d opt for the non-AWD version.
(It should be noted the AWD version has electromagnetic coupling so it is AWD only when it needs to be, with the rest of the time the system is disconnected for fuel efficiency.)
///
BONUS CONTENT: Additive @ Toyota Motor North America R&D
It’s not every day you get a chance to see what’s going on additively at Toyota’s R&D facility in Michigan. . . .

Toyota engineer Matt Mahaffy cleaning and inspecting a prototype part. (Image: TMNA R&D)
A brief look at what they’re doing with additive technology at this important Toyota R&D facility
The team at Toyota Motor North America Research & Development (TMNA R&D) in York Township, MI, is Toyota’s largest R&D center outside of Japan.
Inside the building they perform engineering design and prototype building, vehicle testing and evaluation, technical research, and more. Vehicles like the new 2021 Sienna minivan and the current generation Tundra pickup were developed at the center.
Not surprisingly, they use a lot of additive equipment there.
Here’s a quick look at the approach at TMNA R&D
Nomenclature: On a global level, Toyota uses the term “additive manufacturing.” On the TMNA R&D level they also use “rapid prototyping” (RP) and “3D printing” interchangeably.
Equipment: TMNA R&D has equipment from 3D Systems, EOS, Stratasys and Carbon 3D.
Processes: The additive processes performed at the center include
- Fused deposition modeling (FDM)
- Selective laser sintering (SLS)
- Stereolithography (SLA)
- Multi-jet modeling (MJM)
- Digital light processing (DLP)
Prototypes: They produce scale models and full-size mock-ups for proof-of-concept. Some prototypes are used for appearance confirmation, some for functional checks and still others for workability studies. The models are used to support both traditional vehicle development projects as well as new mobility and advanced development initiatives that Toyota is undertaking.
Tooling: At TMNA R&D they’re producing tooling. An example: process jigs that are used to ensure that the vehicles’ exterior emblems are correctly assembled during pre-production trials at the facility. In addition to which, the jigs are then used in production operations at Toyota North America’s facilities in the U.S., Canada and Mexico.
Production Parts: Not yet. They are currently investigating and developing the means by which they could produce production parts. According to a TMNA R&D spokesperson, “At Toyota we have high standards for part performance and quality that we must consider first and foremost.”
Benefits: The organization is finding that the elimination of long tooling lead time needed to produce parts early in the development cycle is valuable. What’s more, it helps address the related tooling costs associated with early builds.
Challenges: (1) Matching the properties of the materials currently being used in production operations. (2) Being able to scale up additive output to support high-volume production needs.
Driver: At a speech at the 2018 CES Akio Toyoda, president of Toyota Motors and grandson of the founder of the company, said, “It’s my goal to transition Toyota from an automobile company to a mobility company,” and went on say, “I am determined to create new ways to move and connect our customers across the country, across town, or just across the room.” To that end, TMNA R&D is working on advanced mobility solutions—things that just aren’t Camrys or RAV4s. The developers there say that additive manufacturing capabilities are an important tool in advanced mobility vehicle development.
Wishlist: “As with all of our manufacturing processes, we’d love to see higher quality, lower-cost materials and quicker processing speeds,” according to a TMNA R&D spokesperson.
RELATED CONTENT
-
Toyota Finds a Mystery in Occupant Safety for Self-Driving Vehicles
Toyota Motor Co. says its study of how people in self-driving cars react to a near crash proves it will take far more research to improve the safety of occupants in such vehicles, Automotive News reports.
-
Startup Readies Solar-Powered EV
Germany’s Sono Motors GmbH says it has received 5,000 orders for its upcoming Sion electric car, which can be partially recharged by it attached solar panels.
-
Honda Pilots “SmartCharge” Program for EV Owners
Honda Motor Co. is launching a “SmartCharge” pilot program that allows customers to coordinate charging times for electric vehicles and plug-in hybrid for non-peak grid times.