On Developments at Lincoln, Magna, Fiskar, Volvo and More
Lincoln’s plans for electric; Magna and Fisker working together; Polestar in South Carolina; the Volvo XC60 driven; VW gets deep into 3D; Porsche exec on electric; BMW and hydrogen; Staubli cell for tire sensors; and Bridgestone invests in autonomous trucking company.
#interior #robotics
This week On Automotive
- Lincoln’s Electric—and Electrified—Approach
- What “Asset-Lite” Can Do
- Polestar, NW of Charleston, SC
- Meanwhile, Back in Sweden. . .
- VW’s Additive Journey
- Think About This
- Meanwhile, In Bavaria...
- Two Things About Tires
- Audi and the Asterisk
///
Lincoln’s Electric—and Electrified—Approach
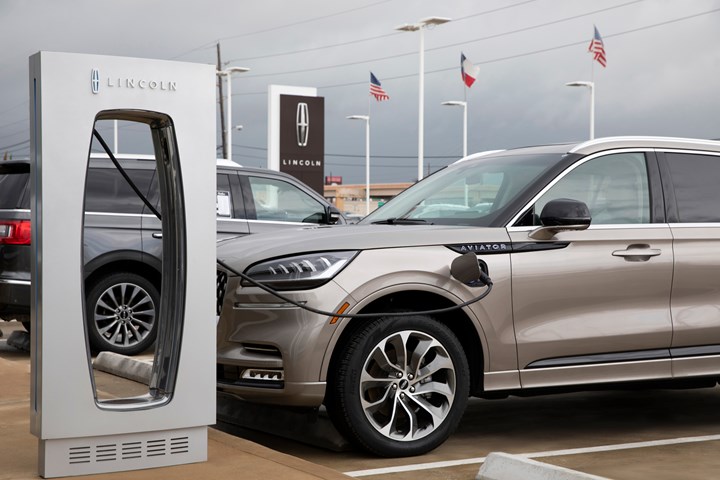
This is a plug-in Lincoln Aviator. Which means it is “electrified.” Fully electric Lincolns are on their way. (Image: Lincoln)
According to Joy Falotico, president, Lincoln, the brand is positioned to have a full suite of electric and electrified vehicles going forward, with the objective of having a global footprint when it comes to its electrified portfolio: “As we accelerate Lincoln’s transformation in North America and China, there is no better time to propel the Lincoln brand forward with electrification.”
John Jraiche, global director for luxury vehicles, enterprise product line management, says that between now and 2030 the brand will have four new electric vehicles on a rear-wheel drive/all-wheel drive platform.
Defined
So a bit of definition is necessary.
“Electrification” generally means hybrid vehicles.
So, for example, there is the Lincoln Aviator Grand Touring, which is a plug-in hybrid.
There is a 400-hp twin-turbo V6 and 10-speed automatic in the Aviator Grand Touring. . . but also a 75-kW permanent magnet electric motor (called a “Nano Electric” motor because, probably, that sounds techy). The total system output is 494 hp. There is a 13.6-kWh lithium ion battery pack. The vehicle can be charged by Level 1 (120-v) or Level 2 (240-v) chargers.
The non-hybrid AWD Aviator gets an EPA estimated 17 city/24 highway/20 combined miles per gallon.
The hybrid AWD Aviator gets 54 city/58 highway/56 companied MPGe.
Then there’s “electric.” Which means what you think it does. As in “battery electric vehicle” (BEV).
The Platform
The platform that Jriache mentions is one that was developed by Ford and will be used for its vehicles, as well. Scale matters.
Hau Thai-Tang, Ford's chief product platform and operations officer, described the platform at it May 26 Capital Markets Day:
“Our new rear-wheel drive all-wheel drive BEV flexible architecture will underpin a range of motor vehicles slated for production between now and 2030, including active lifestyle vehicles with great driving dynamics. Cargo vehicles for those who value space and versatility for their commercial needs. Pickups delivering legendary built for tough capability on mid-sized trucks. Rugged SUVs for our adventure-seeking customers. And high margin, high demand larger two and three-row SUVs for families around the world like Explorer and Lincoln Aviator, all from this one flexible architecture.”
Know This: By 2025, Lincoln expects half of its global volume will be zero-emissions vehicles; its entire portfolio will be electrified by 2030.
It will introduce an electric vehicle next year: Which will mark its 100th anniversary.
///
What “Asset-Lite” Can Do
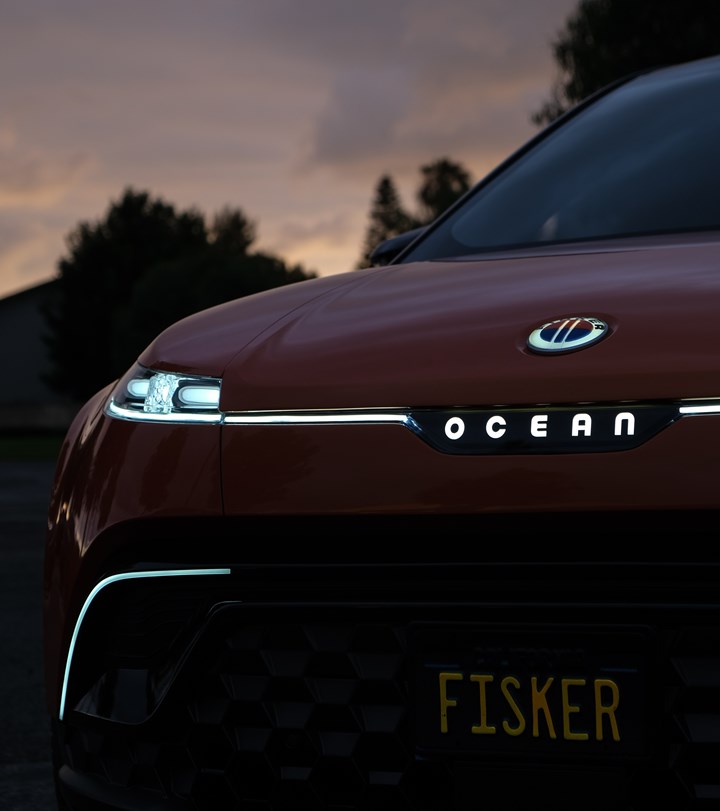
The Fisker Ocean electric crossover will be manufactured for Fisker by Magna. Magna also worked on the platform being used for the vehicle. (Image: Fisker)
“Our complete vehicle systems approach, combining all elements of our portfolio, makes Magna’s proposition highly competitive – in capital efficiency, launch reliability and speed to market,” said Magna Steyr President, Frank Klein.
Efficiency. Launch reliability. Speed to market. Sounds like a trifecta.
Magna Steyr is a contract manufacturer that has produced more than 3.7 million vehicles, 30 different models. It is presently producing the Mercedes G-Class, the BMW 5 Series and Z4, Jaguar I-Pace, and Toyota GR Supra.
And on the calendar for November 17, 2022, at the Graz, Austria, facility is the SOP of the all-electric Fisker Ocean SUV.
Fisker chairman and CEO Henrik Fisker says the company has a “asset-lite” model.
As in it won’t own assets like factories.
So it will work with Magna on the Ocean.
More Than Manufacturing
It is worth noting that the Ocean will be based on an electric vehicle architecture. . .that Magna developed—but Fisker modified.
The aluminum-intensive platform—code-named “FM29”—helps provide a cost-effective product: It is expected that the starting MSRP for the Ocean in the U.S. will be $37,499.
///
Polestar, NW of Charleston, SC
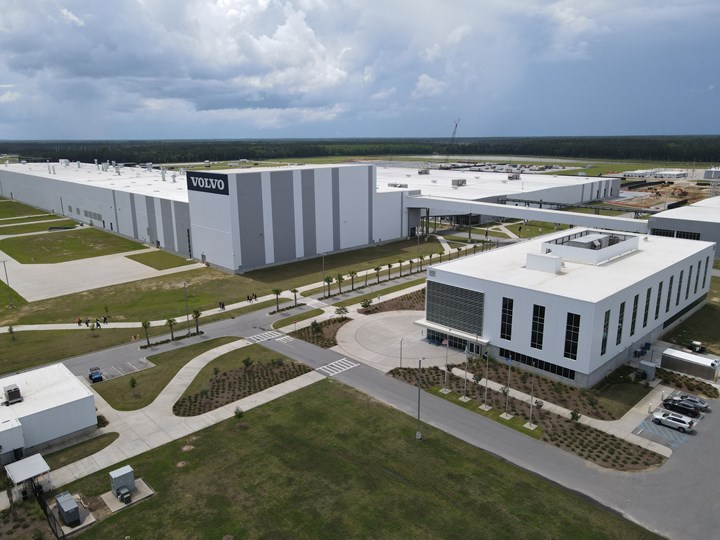
The Volvo assembly plant in South Carolina is located northwest of Charleston. It is being expanded to accommodate production of the Polestar 3. (Image: Volvo)
Speaking of making electric vehicles. . .
But this one isn’t “asset-lite.”
Volvo is investing $118-million into its factory in Ridgeville, South Carolina. . . yes, Volvo has a 2.3-million square foot plant on 1,600 acres. It includes a body shop, paint shop, and final assembly facility that, with the aforementioned money, represents a $1.2-billion operation.
The additional $118 million is preparing the plant to produce the Polestar 3.
The Polestar 3 will be an electric SUV.
At present they’re manufacturing the Volvo S60 in Ridgeville. It is powered by a gasoline engine (although there is a plug-in hybrid available, too). And it is a sedan, not an SUV.
Next Gen. Next Evolution
The Polestar 3 will be built on a next-gen electric architecture that Volvo, which is an affiliate of Polestar (Polestar was established in 2017 by Volvo and Geely Holding), is developing.
That, and that it will feature “the next evolution of Polestar’s design language” and use the Android Automotive OS (as the Polestar 2 does), is all that is known about the vehicle.
But as for the expansion of the plant, here’s Dennis Nobelius, Polestar COO:
“Production in the USA makes procurement more efficient, reduces delivery times and will even have a positive impact on the price of the Polestar 3 SUV. All of this makes the brand even more competitive in the critical American sales market.”
Polestar reckons that the U.S. and China are the two big EV markets.
So it will be producing the Polestar 3 in China, too.
///
Meanwhile, Back in Sweden. . .
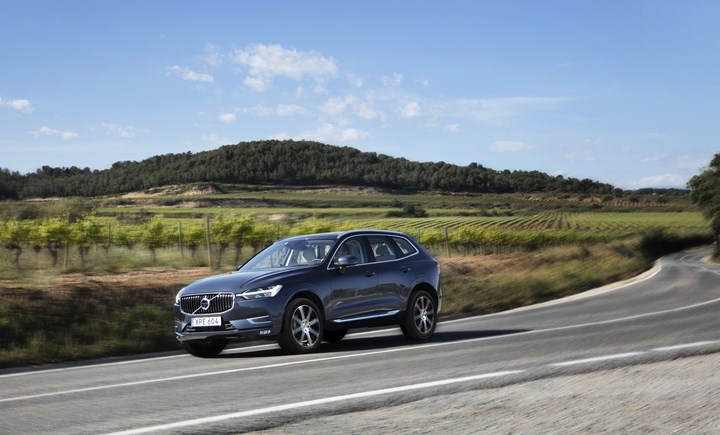
The Volvo XC60. Inside there’s a sense of Sweden. (Image: Volvo)
Of course, odds are when you think of “Volvo” you think of Scandinavia, not South Carolina. Perhaps to the level of Sweden. Perhaps to the granularity of Gothenburg.
Which is where the 2021 XC60 T5 AWD Momentum hails from. It’s a lux compact SUV.
In terms of styling, from the front it is unmistakably a Volvo. The “Thor’s hammer” headlamps. The badge—the circle with the arrow pointing upward to the right, a.k.a., the symbol for iron, which was presumably used because the company, back in 1927, when it was established, wanted to assure the public that its cars were solid like iron and therefore safe. The overall stance of the SUV.
The rear view, with the signature lighting going up into the D-pillar, is similarly Volvo.
And what’s interesting is that those two lighting elements—fore and aft—are visible in the side view, so while there are plenty of SUVs that pretty much resemble one another when seen from the side, the lighting helps telegraph the message of what this vehicle is.
Swedish Furniture
On the inside, everything is appropriately ergonomic in terms of reach and knobs. The 2021 model has a 9-inch infotainment screen running something called “Sensus Connect,” which seems dated and is being replaced in the ’22 model with an Android system. (Sensus Connect has both Apple CarPlay and Android Auto; the new system is an Android OS, which offers Apple CarPlay and Android Auto).
One of the most wonderful things I’ve seen in an interior in a long time is the cloth used for the seats. Yes, there is leather available. But the “Textile” box is the one I’d check because it is a fresh approach that complement the interior design in a way that leather simply doesn’t.
It seems more Swedish.
///
VW’s Additive Journey
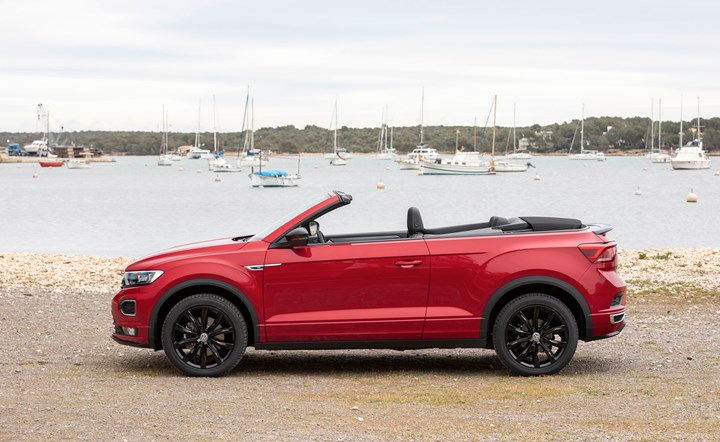
A-pillars for the VW T-Roc Cabriolet (not available in the U.S.) have been 3D printed and are undergoing testing to determine whether they can be made additively in production. (Image: Volkswagen)
Dr. Martin Goede, head of Technology and Planning and Development, Volkswagen, announced in September 2018, “Automotive production is facing major challenges: our customers are increasingly expecting more personalization options. At the same time, complexity is increasing with the number of new models. That’s why we are relying on state-of-the-art technologies to ensure a smooth and fast production. 3D printing plays a particularly important role in manufacturing of individual parts.”
The parts being produced back then, however, were not exactly the sorts of things that might make you sit up and take notice.
Gear knobs. Key fobs. Tailgate lettering.
But the folks in Wolfsburg were nothing if not aggressive.
In December 2018 the company announced that it had been working with HP on the development of binder jetting technology. So they started using both selective laser melting (SLM) and binder jetting.
The company established a 3,100-square meter additive center in Wolfsburg.
It began using the gear for toolmaking.
COVID & Beyond
In the April 2020 the companies of VW Group—from Audi to Volkswagen Motorsport—took their 3D printing capability and joined a European effort with Airbus and “Mobility goes Additive,” a network of some 250 companies, to produce PPE in response to the COVID-19 pandemic.
And in June 2021, Christian Vollmer, member of the Board of Management of the Volkswagen Brand responsible for Production and Logistics, announced, “Despite the ongoing challenges of the coronavirus pandemic, we’re continuing to work on innovation. Together with our partners”—in this case the partners being Siemens, which is providing software, and HP, the equipment—“we aim to make 3D printing even more efficient in the years ahead and suitable for production-line use.”
Production Line
The first step is the binder jetting of A-pillars for the cabrio version of the T-Roc, a subcompact sport ute.
The parts are produced in Wolfsburg. Presently there are 15 industrial printers on site there, in addition to desktop printers in various departments.
(To give you a sense of the footprint of the Wolfsburg facility: it is approximately the size of Monaco. In addition to the massive production halls there is the Technical Development center: 11,000 employees working in a 1.2-square kilometer facility.)
There are plans for more printers.
Back to the A-pillar
The first printed A-pillars are undergoing testing at the VW facility in Osnabrück.
“But why A-pillars?” we asked VW.
“The parts have a high lightweight potential,” was the response, with a mass savings on the order of 50% compared to sheet metal versions. “The high requirements of the parts”—remember, this is a convertible version of the T-Roc, which means the A-pillars have a non-trivial role to play—“gives us the chance to develop the complete process chain from idea, part design, simulation, production, testing, and quality, to certification.”
A Thought: Although A-pillars aren’t geometrically complex like many of the example parts that are shown by 3D printing companies, it is reminiscent of the lessons learned by some OEMs in the early days of robot deployment. Rather than going for simple jobs, the robots were put in difficult situations. And generally didn’t work so well. By starting with things like A-pillars VW will be able to garner invaluable knowledge that will help it scale its capabilities.
It plans to produce 100,000 3D printed components per year in Wolfsburg by 2025.
///
Think About This
"The battery cell is the combustion chamber of the future.”--Oliver Blume, Chairman of the Executive Board at Porsche
///
Meanwhile, In Bavaria
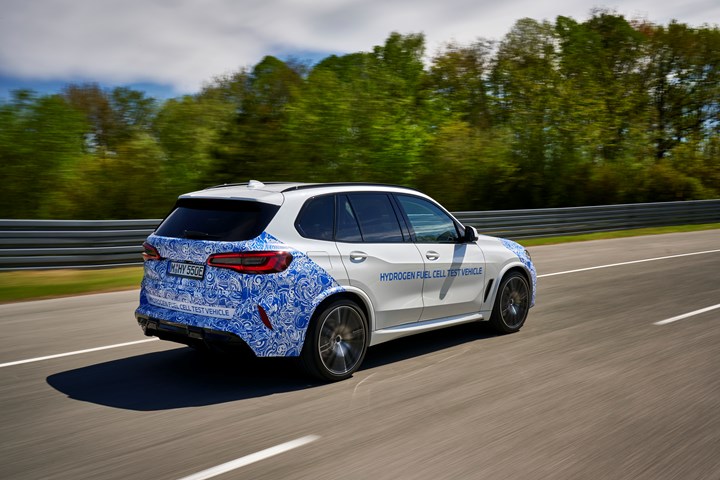
BMW is testing fuel cell vehicles on the road. The company sees it as an alternative to battery electric vehicles. (Image: BMW)
BMW is putting “near-standard” vehicles on the road that are equipped with its i Hydrogen NEXT system onboard.
That’s right: A fuel-cell technology.
“Hydrogen fuel cell technology can be an attractive option for sustainable drivetrains—especially in larger vehicle classes,” said Frank Weber, member of the Board of Management of BMW AG responsible for Development.
Toyota, Too.
The cells for the vehicles are sourced from Toyota, with which BMW has a product development program. The fuel cell stack and drive system are strictly BMW.
Fuel Cell 101
Hydrogen is stored in two carbon fiber reinforced plastic 700-bar tanks. Six kilograms are contained. It requires three to four minutes to fill the tanks.
There is a chemical reaction between the hydrogen and the oxygen in the air. In the BMW system this results in the generation of 125 kW of electricity (and water vapor).
The electricity is then used to power an electric motor to drive the wheels.
In addition to which, there is a buffer battery that stores energy that is generated during coasting and braking. It is used during hard acceleration.
The system output is 374 hp—as much as the most powerful BMW six-cylinder engine.
Soon Real
BMW anticipates that it will have an X5-based vehicle powered by i Hydrogen NEXT tech in low production volumes by late 2022.
///
Two Things About Tires
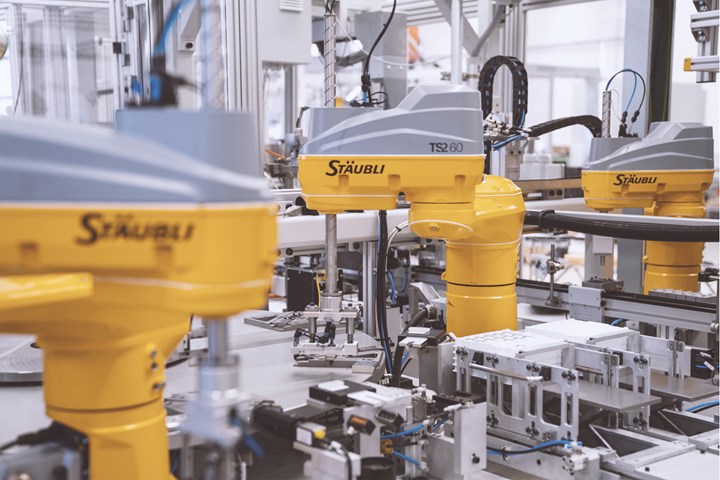
1.
An assembly line capable of producing four million tire pressure sensors per year has been developed by MMS Modular Molding Systems GmbH of Berndorf, Austria, for BH Sens, a Chinese supplier and joint venture between Baolong and Hülsbeck & Fürst. Included in the assembly are three Stäubli SCARA robots. Why SCARAs rather than six-axis robots? Because the movement of the components is done in four axes, so the six-axis equipment was deemed to be too slow.
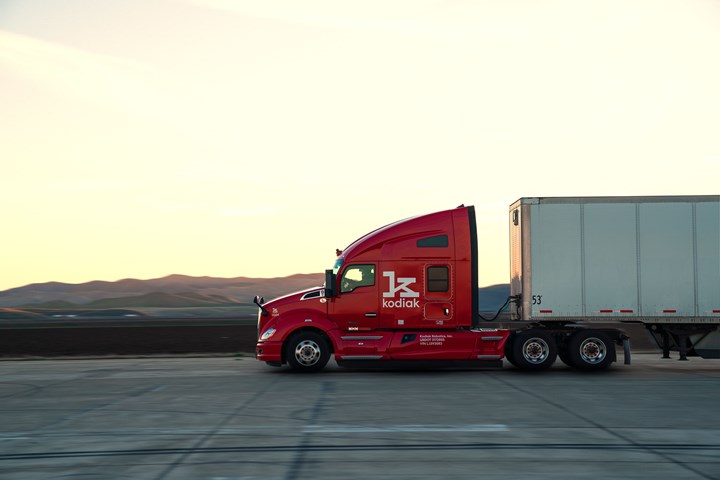
2.
Bridgestone Americas has taken a minority investment in self-driving trucking company Kodiak Robotics, which operates a fleet of Level 4 self-driving long-haul trucks to move freight in Texas.
(There are safety drivers on board the trucks now. Plans are to go autonomous in the next few years.)
Bridgestone’s rationale was explained by Paolo Ferrari, Global Chief Solutions Officer, Bridgestone Corporation, and President & CEO, Bridgestone Americas:
“Advancements in tire-centric technologies are critical to unlocking greater innovation in mobility, while also delivering significant sustainability benefits. This investment will enable Bridgestone and Kodiak to work together to co-develop advanced mobility solutions with speed and precision that will revolutionize commercial trucking.”
///
Audi and the Asterisk
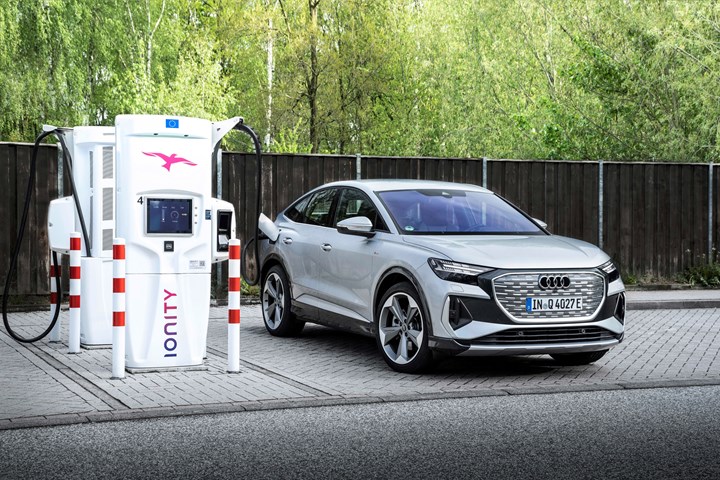
Audi Q4 Sportback 50 e-tron quattro. An electric Audi. (Image: Audi)
Audi CEO Markus Duesmann made a rather important announcement at a climate conference in Berlin this week:
Beginning in 2026 the only vehicles that it will launch globally will be electric.
What’s more, Duesmann said the company will phase out production of internal combustion engines by 2033.
*
But then there’s the asterisk.
While Audi will only globally launch new EVs, not every vehicle is a global vehicle.
It can be a different story for regional markets.
And there is one massive, important regional market for Audi: China.
So while the production of internal combustion engines in general will be discontinued by Audi by 2033, the company acknowledges: “*China is an exception.”
And while Audi isn’t planning to develop new internal combustion engines, Duesmann said that they’ll continue to work on the engines up until the end:
“Audi’s last internal combustion engine will be the best we’ve ever built.”
RELATED CONTENT
-
on lots of electric trucks. . .Grand Highlander. . .atomically analyzing additive. . .geometric designs. . .Dodge Hornet. . .
EVs slowdown. . .Ram’s latest in electricity. . .the Grand Highlander is. . .additive at the atomic level. . .advanced—and retro—designs. . .the Dodge Hornet. . .Rimac in reverse. . .
-
Printing a Shock
Although this shock absorber is just a demonstration device, its fabrication is rather clever as the materials company that made it, Covestro, used three different materials and three different 3D fabrication processes to make it: First, there’s the outer spring of the 40 x 7-cm part.
-
How GM Quickly Created Capacity for Mask Production
GM’s head of global manufacturing engineering talks about how a global team put mask production capacity on the floor in a week