Global Supply of Automotive Fasteners from a Single Source
PennEngineering offers a global supply for a wide range of fasteners for the automotive industry, including China-based facilities that manufacture standard and custom products to world-class standards of quality at lower cost.
According to Toyota, there are some 30,000 parts in a car. What holds most of them together are the hundreds of fastener types that come from suppliers all over the world. As automotive OEMs, Tier 1 and aftermarket suppliers seek to streamline their supply chains, there is tremendous value in finding vendors that can provide a wider array of products and support those products globally with local distribution and engineering services. A major player like this in the fastener category is PennEngineering, which makes hundreds of different fasteners for the automotive industry with standard and custom products as well as automated assembly solutions.

PennEngineering is among the world’s largest providers of fastening solutions for the automotive industry.
Headquartered in Danboro, PA, PennEngineering also has large operations in Michigan, Germany, Ireland, China and Singapore. From each of these bases, the company provides application engineering, custom design and prototyping, assembly engineering services and testing facilities.
PennEngineering’s automotive business is comprised of two business units that the company refers to as Mechanically Attached Fasteners (MAF) and PennAuto™, a wholly-owned subsidiary based in Kunshan, China.

Mechanically Attached Fasteners
Mechanically attached fasteners are used to permanently and securely attach threaded, reusable fasteners to automotive parts or panels. PennEngineering’s MAF types include structural riveted fasteners, self-clinching fasteners, and blind threaded inserts. In addition, the company designs and manufactures automated feeding equipment for these fasteners in die press shop applications and assembly line solutions to meet different production requirements.

There are several advantages to MAF-type fasteners. They are strong, relatively light, quick to install, and they lend themselves well to automated assembly. They can hold a wide range of sheet metal thicknesses with a single nut type and can be applied to different materials, even carbon fiber parts. They can be finished with almost any kind of surface coating.
Structural Riveted Fasteners

As the word “rivet” implies, these fasters are pressed into a part with a die set that forms the fastener metal on the back side and/or the workpiece material to permanently lock the faster in place. Represented by the company’s PROFIL® brand, these fasteners are ideal for securely joining sheet metal structures of different materials, and come in the forms of threaded nuts and studs. That these types of fasteners are also widely used in aircraft applications speaks to their reliability. In automotive assembly applications they are commonly used on body panels, seating, instrument panels, controls, safety systems and enclosures.
Self-Clinching Fasteners
The original PennEngineering product, PEM® brand self-clinching fasteners have been used in the automotive industry for over 75 years. With this type, the fastener is pressed into the part, displacing the host material around the mounting hole, causing it to cold flow into a recess in the shank or pilot of the fastener. (See self-clenching nut insertion animation.)

These fasteners are still so widely used because they provide strong, reusable threads in thin metals with high push-out and torque-out resistance. Moreover, they are highly efficient and inexpensive to use in high-volume, automated assembly operations. PEM brand fasteners come in a wide variety of configurations including nuts, cable tie mounts, studs and pins, standoffs, weld nuts and more. There is even a fastener based on this technology, the VARIMOUNT® bonding fastener, designed to fasten different materials such as composites, plastics, metal, or almost any other rigid material.
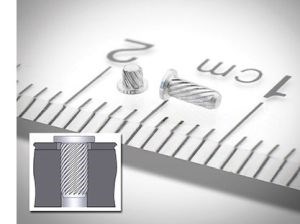
Ideal for automotive electronics, MicroPEM® brand fasteners utilize self-clinching, broaching, flaring, surface mount, or weld technology to provide strong, reusable and permanent threads. They also provide mounting points in thin sheet metal, printed circuit boards, and other thin materials. With pin diameters and standoff lengths as small as 0.7 mm, these tiny inserts can accommodate an M1 fastener, the smallest ISO-designated M-profile, and clinch flush into sheets as thin as 0.3 mm.
Blind Threaded Inserts

The ATLAS® brand of blind threaded inserts provide strong and reusable, permanent threads in sheet materials where only one side is accessible for hardware installation. Also known as rivet nuts or blind threaded rivets, there are three main types: SpinTite®, MaxTite® and Plus+Tite® fasteners.
The SpinTite types are used for most applications where strong threads are required for blind applications. They are installed from one side using a spin/spin technique (see spin/spin insertion animation). In addition to high thread and torque-out strength, these fasteners have minimal inventory requirements since each size can accommodate many material thicknesses.
The heavy duty MaxTite® types are designed for the most demanding applications. They are installed from one side using a “spin/pull” technique.
The blind Plus+Tite inserts feature a slotted body that folds into four petals upon installation, gripping the backside of the parent material. These inserts can be installed into single, variable or multiple thickness materials.
PennAuto
PennAuto fastener products offer a unique manufacturing and distribution methodology based on making high-strength components and fasteners in PennEngineering’s wholly owned subsidiary in Kunshan China. Supported by sales, product inventory, distribution services and customer technical assistance, PennAuto facilities are strategically located in close proximity to its global customers.

View PennAuto's Kunshan China factory video.
PennEngineering is one of the first companies in the world to develop the ability to manufacture high-strength, complex components and fasteners in China that meet today’s global automotive quality standards. PennEngineering can produce PennAuto hardware with complex geometry using cost-effective and advanced processes unlike those typically employed conventional machining methods. PennEngineering utilizes highly-controlled, multi-process, high-volume production techniques, which involve forming or forging of the basic fastener followed by precision secondary turning or machining operations to complete the job.
This capability uniquely positions PennEngineering to deliver product at a lower cost while achieving the same or improved levels of quality, as compared with Western competitors who are locked into high manufacturing and distribution cost structures.
Wherever in the world automotive vehicles and components are manufactured, PennEngineering aims to be their go-to resource for automotive fastening solutions. For more information, go to the PennEngineering website to ask a technical question, find a local representative, global contact or email at info@pemnet.com.
RELATED CONTENT
-
Increasing Use of Structural Adhesives in Automotive
Can you glue a car together? Frank Billotto of DuPont Transportation & Industrial discusses the major role structural adhesives can play in vehicle assembly.
-
Choosing the Right Fasteners for Automotive
PennEngineering makes hundreds of different fasteners for the automotive industry with standard and custom products as well as automated assembly solutions. Discover how they’re used and how to select the right one. (Sponsored Content)
-
Ford Copies Nature
As Nature (yes, capital N Nature) has done a pretty good job of designing things, it is somewhat surprising that Man (ditto) doesn’t follow Nature’s lead more often when it comes to designing objects.