on Plenty of Things about Volkswagen & Other Topics, Too
On VW’s Project Trinity, transformation of product development and the interior of the ID.Buzz; new buses of interest; carbon fiber for wheels and accessories (non-automotive); and Aston Martin’s EV battery
#workforcedevelopment
VW Spending Billions on New EV Plant in Wolfsburg
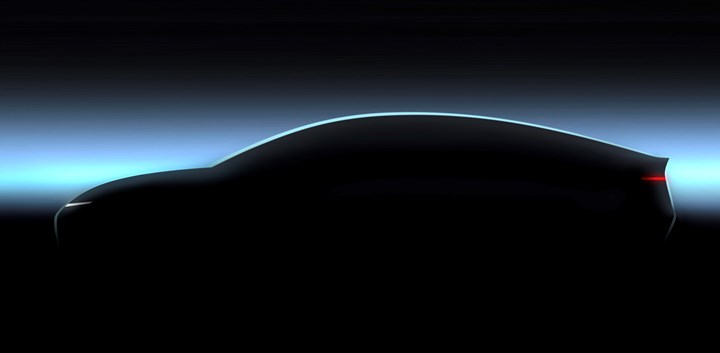
This vehicle is said to be the VW Trinity—but for Volkswagen “Trinity” encompasses much more than a sedan. (Image: VW)
Volkswagen is investing some €2-billion to build a new manufacturing facility in Wolfsburg to produce the Trinity, a net-carbon neutral electric vehicle.
It will go into production in 2026.
It is based on the SSP platform (see following item).
Notably, VW says that the Trinity production operations will set standards for the company.
For example, it expects production time of 10 hours per vehicle.
How will this be achieved?
- Fewer variants
- Fewer components
- More automation
- Leaner production lines
- New logistics concepts
Dr. Christian Vollmer, Member of the Board of Management of the Volkswagen brand responsible for Production:
“We are focusing on innovative and sustainable manufacturing concepts. Building a new factory in Warmenau [a district in Wolfsburg] also gives us the opportunity to make the existing factory fit for the future, step-by-step and from top to bottom. Trinity stands for a completely new kind of thinking, production, collaboration. It takes courage to shape the future. This is how Wolfsburg will become the yardstick for innovative production concepts – for Volkswagen and the entire industry.”
Volkswagen will start building the ID.3 in the main Wolfsburg facility in 2023. That plant is undergoing modification to permit that.
Trinity
When Project Trinity was announced last year, it wasn’t just the name of the electric sedan that’s teased in the image above.
The company announced three themes (Trinity: get it?):
- A new electronics platform with advanced software (see the next item if you already haven’t)
- A simplified supply structure
- Networked and intelligent production (a.k.a., Industry 4.0) in Wolfsburg
Yes, manufacturing is part of the thinking as the company begins to be more oriented toward software.
///
VW PD Transformation
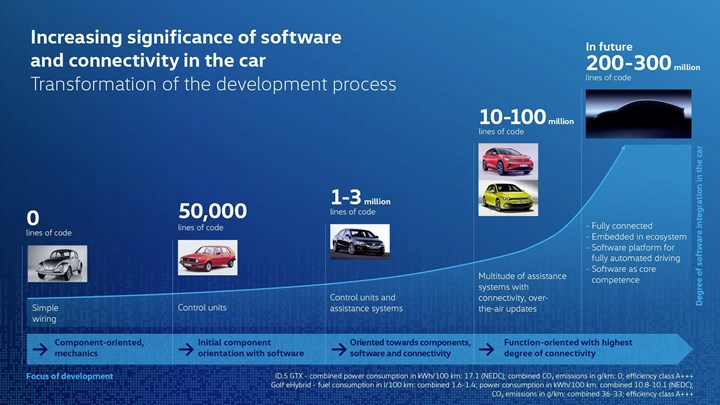
If you’ve ever wondered about the amount of code in a vehicle, here’s your answer. (Image: VW)
“If the car is increasingly becoming an electrically driven software product, then its development must also evolve in all dimensions. We are making TD [Technical Development division] more connected and more efficient by focusing our processes and organization on systems and functions rather than on components.
“Software first rather than hardware first.
“This will enable us to cut development times by 25%. In the future, vehicle projects will be completed in 40 months from the point at which the basic software architecture is in place instead of 54 months, as before.”
So says Thomas Ulbrich, member of the Board of Management responsible for Technical Development, Volkswagen Group.
Volkswagen has 11,500 employees in its TD operation. It is the group’s largest engineering unit.
There are several elements to the redesign of the development process.
- Systems Engineering. Historically there was a focus on the development of discrete components. This will give way to a focus on functions and systems. This is not just considering the vehicle in the context of itself, but the vehicle in relation to the entire ecosystem that it exists within, which means other systems developed by other companies.
- Functional Integration. Personnel from a variety of different functional areas will be working together at an 800-million Euro facility being built in Wolfsburg, Campus Sandkamp. The facility, which is to be complete in five years, will house some 4,000 employees. This will be the lead operation for product development and include design, conceptualization, UX, product strategy, model series, and technical project management and team members. There will be representation from Purchasing, Finance, Production Planning, Quality Assurance, and Sales.
- Training. Lots of training. There is a recognition that the transition to the focus on systems and functions is not going to be within the wheelhouses of many of its employees, so VW is addressing this through training. VW expects to reskill some 4,000 employees and up-skilling as many as 8,000 more. The curriculum is varied, from short courses to those lasting up to 180 days. The type of training that VW is performing is not trivial. The company suggests, for example, “a skilled metalworker could become an automotive engineering specialist.”
A major focus of TD is the development of a new platform, Scalable Systems Platform (SSP), for its electric vehicles. SSP will combine the existing MEB and PPE platforms. It will potentially be the basis of more than 40-million VW Group vehicles.
///
ID.Buzz and an Approach to Interiors
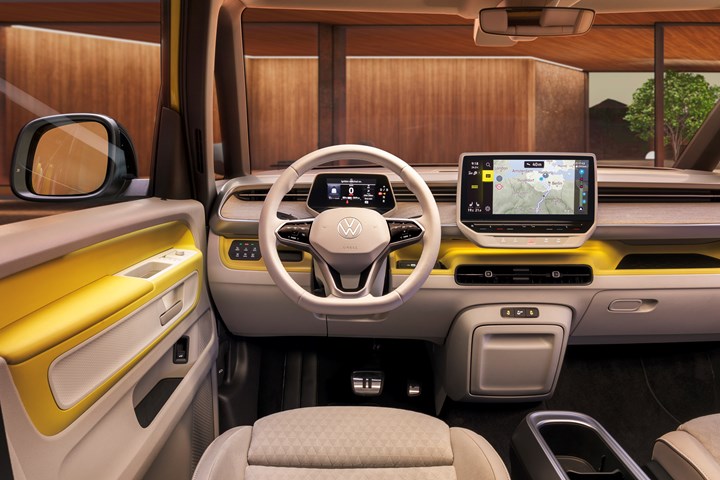
At this risk of turning this into a VW-centric newsletter. . .
By now you’ve undoubtedly seen, in other outlets, information about the VW ID.Buzz.
So there is little point in rehashing much of that.
And it is somewhat interesting to know that by VW’s own admission, the vehicle harkens back to a vehicle introduced 72 years ago, the T1 (“With the ID. Buzz, we are transferring the T1 DNA to the present day and thus into the era of electric mobility and sustainability”—Jozef Kabaň, Head of Volkswagen Design); the vehicle was shown in concept form five years ago at the North American International Auto Show in Detroit; and while it will become available in Europe in 2023, it won’t come to the U.S. until 2024.
So there’s little need to hurry.
But there is something that caught our eye about the ID.Buzz.
Marine Waste Redux
As you may recall from last week’s on Automotive there was a piece about a material made with recycled plastic from marine waste.
Volkswagen announced that the interior of the ID.Buzz contains no leather or other materials of animal origin.
One of the fabrics on the internal is made with SEAQUAL yarn.
And we’ve learned that there is the SEQUAL Initiative, which “is a community of individuals, organizations and companies working together to help clean our oceans, raise awareness of the issue of marine litter and highlight those helping to fight it”.
It “works with the waste management and recycling industries to transform marine litter into SEAQUAL® MARINE PLASTIC, so that leading brands and manufacturers can create inspiring sustainable products.”
The yarn used in the ID.Buzz consists of ~10% marine plastic and ~90% recycled PET bottles.
The upholstery in the electric van is “ArtVelours ECO,” which is made with 71% recycled polymers.
Note: While it seems absolutely appropriate for a zero-emissions vehicle to contain reduced-carbon materials, there is conceivably something bigger happening: The use of these materials will likely become more wide-spread as there is greater familiarity with them—or, looked at another way: as people don’t discern any difference between them and more traditional cow-based fabrics.
///
EV Bus Developed in Canada
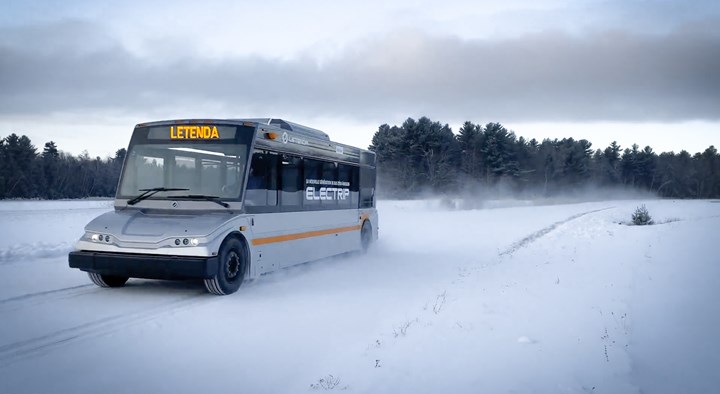
An electric bus developed with Canadian winters in mind. (Image: Letenda)
When it comes to personal transportation, there is very little in the way of vehicles that are purpose-built. After all, general architectures (e.g., pickup, sedan, SUV) are meant to sell in vast quantities.
In the commercial space there is more of a focus on what the vehicle will be used for, so more in the way of tailoring vehicles for the application.
And to that end, Letenda, a company based in Longueuil, Québec (a suburb of Montreal), has developed what Nicolas Letendre, president and CEO, describes as “an electrically powered city bus designed to withstand winter temperatures.”
It gets cold in Quebec.
The 30-foot bus, which can accommodate 45 passengers, is powered by a Cummins electric powertrain system, including the controls, batteries (222-kWh Li-ion NMC in three packs), propulsion motor, power electronics, charging controls and connectivity systems.
The bus is aluminum-intensive; Rio Tinto Aluminum contributed $650,00 to Lentenda for the development of the Electrip. (The company also obtained support from an array of other companies and government agencies.)
Maneuverability is enhanced by a steerable rear axle.
Accessibility is facilitated by a low load floor—which happens to feature radiant heating, which is certainly key in the cold climes of places like Quebec.
///
Hydrogen on the Road
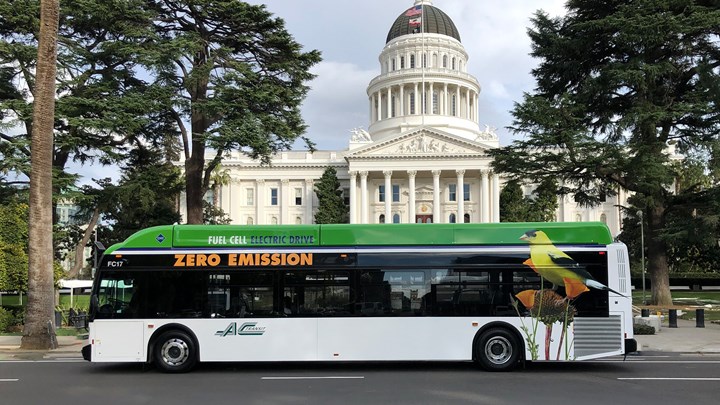
Powered by hydrogen. (Image: New Flyer)
While on the subject of buses. . .
Seems that buses are in some ways have more variety propulsion-systems than light vehicles.
“With over 50 years of experience manufacturing zero-emission transit buses, our Xcelsior CHARGE H2 bus is a game changer for North American operators. Not only does it reduce greenhouse gas emissions, but it also delivers extended range, fast fill times, and no reduction in performance from beginning to end of life,” says Ben Wood, vice president, Supply Management, New Flyer.
The System
The Xcelsior CHARGE H2 is powered by a fuel cell system (a Ballard FCvelocity-HD85). Forty-foot versions of the bus have 37.5 kg hydrogen storage capacity and have a refueling time of from 6 to 10 minutes. The 60-foot version of the bus has a 60 kg hydrogen capacity and a 12 to 20 minute refueling time.
The fuel cell recharges the on-board battery system. The equivalent battery energy for the 40-foot bus is 700 kWh; it is 1,100 kWh for the 60-footer.
The electric drive system for the 40-foot bus is a Siemens ELFA2; it provides 160 kW. The 60-foot bus has that drive system as well as a ZF AVE 130 in-wheel motor center drive axle. It provides 320 kW.
These hydrogen buses just aren’t something that New Flyer has in its portfolio that it can point at should anyone ask.
Some Numbers
Hexagon Purus, a supplier of high-pressure hydrogen storage tanks to New Flyer, has announced it received a $2-million contract from the bus manufacturer for tanks to be delivered in 2022.
Hexagon Purus says it delivered tanks to New Flyer last year for just under 30 buses.
In addition to fuel cells, New Flyer offers its Xcelsior line with battery-electric, CNG, hybrid and diesel propulsion systems.
(A gratuitous thought: One thing that seems to be overlooked in the powertrain transition for passenger vehicles is that there are different requirements predicated on different conditions. Clearly the range of offerings of New Flyer indicates that this isn’t the case in buses.
(While zero emissions may be the goal, doesn’t it make sense for organizations and individuals to have access to systems that will fulfill their needs while providing emissions-reductions as the technologies are developed to make “zero” something that is suitable (and affordable) for wide-spread deployment?
(That is: the approach being taken is binary. It either is a gasoline engine or an electric motor. But what about hybrids and plug-ins, systems that provide both? Certainly, the emissions aren’t zero, but they are better than that of a comparably powered vehicle that runs on gasoline alone.)
///
A Lot of Carbon Fiber (Wheels)
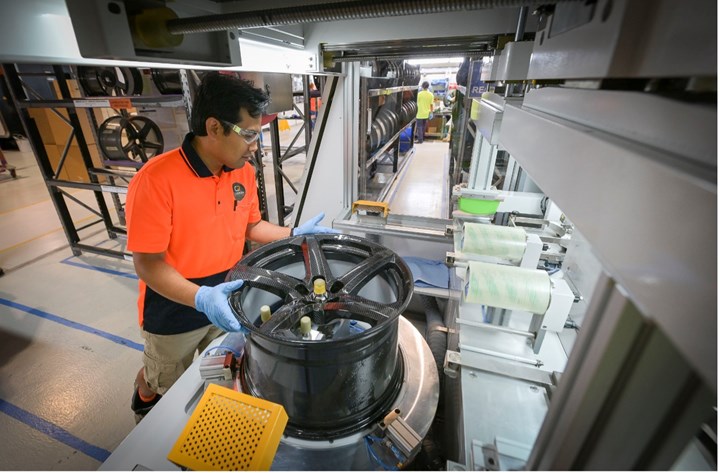
Carbon fiber wheels can provide a significant weight-save, even compared with aluminum. (Image: Carbon Revolution)
Carbon Revolution—a supplier based in Geelong, Australia—announced last week that it has sold its 50,000th single-piece carbon fiber wheel.
That wheel will be fitted to a Corvette Z06.
The wheel producer has contracts with General Motors, Ford and Ferrari for its wheels. There are six programs in production with those OEMs and nine in development.
Of those development programs, four are for EVs.
About that 50,000th
“The reason Carbon Revolution is able to achieve low mss yet highly durable wheels is that the wheel structure is made entirely from carbon fiber,” Ashley Denmead, Director of Engineering for the firm, tells on Automotive.
He adds, “There are many other proprietary elements to this wheel, including a plasma-applied thermal barrier coating which protects against cases of misuse that may cause brake rotors and discs to overheat.”
After all, the Corvette Z06, with its 670-hp, 5.5-liter, naturally aspirated V8 is engineered for the track, so braking is as important as accelerating. It has Brembo carbon ceramic brakes.
Making Them
In terms of manufacturing the wheels, Denmead says, “The manufacturing process requires precise fiber layup and high-pressure molding which must have zero imperfections of fiber and resin. All wheels are assessed through X-ray CT scanning to assure high quality.”
Although Denmead won’t say what the wheel weighs, there’s this: “The carbon fiber wheels weight savings are over 41 pounds, or a roughly 40 to 50% reduction, versus the standard forged aluminum wheels.”
(Note: If you’re interested in composites, know that there is a sister publication to this that covers all things composites, CompositesWorld, which you should check out.)
///
Remarkable Recycling
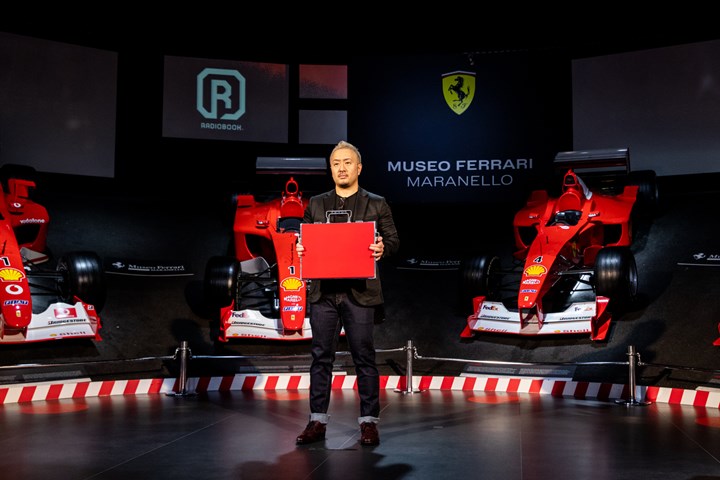
From Formula One cars to. . .briefcases. (Image: Radiobook)
Formula One teams lots of money to proverbially grease the wheels. Sponsorship is a key source, of course.
Scuderia Ferrari has an array of sponsors—Shell, AWS and Ray-Ban among them.
And some less well-known outfits, like Japan-based Radiobook.
One of the things Radiobook does is create new products by reusing materials from various sources.
Like Scuderia Ferrari.
For its line of Renascence business accessories—including a briefcase, iPhone case, business card holder—it uses scrap from the construction of the Ferrari F1-75 race car.
The carbon fiber pieces are formed into the appropriate configurations for the object then transformed using the Wajima-nui lacquerware method.
These products—like the F1-75—are art and engineering.
And also like the F1-75, not inexpensive.
The attaché case shown in that photo?
$61,899.
///
The Aston Martin of Batteries
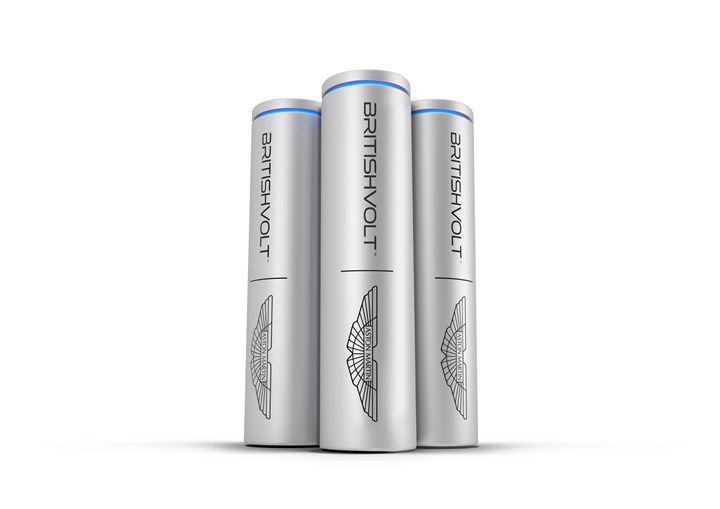
Bespoke batteries being developed for Aston Martin. (Image: Aston Martin)
Quick: What brand of 12-volt battery do you have under your hood?
I don’t know what’s under mine, either.
One might imagine that the performance of a given EV is largely predicated on the motor and the software. Of course, the EV battery has a role to play in things like everything from range to recharge time.
But not something that would cause someone to say, “So, what kind of battery do you have in your new Electrozoom? My Sparkatron 600 has a new Sparkatronic battery pack 2.0 and it’s the best.”
Which leads to an announcement that luxury car maker Aston Martin and Britishvolt, a UK-based developer of lithium ion batteries, have signed a Memorandum of Understanding for the development of batteries for Aston Martin.
An objective is to “develop bespoke high performance battery cell technology.”
According to Tobias Moers, CEO of Aston Martin Lagonda, “Working together with Britishvolt, I believe we can create new technologies to power benchmark-setting Aston Martin electric cars that will match our reputation for high performance and ultra-luxury with the highest standards of sustainability.”
To be sure, battery chemistries have a notable impact on sustainability, but does Aston’s “reputation for high performance and ultra-luxury” really depend on batteries?
(Yes, yes, assuming there is an above-average range and charging capability of said battery.)
In a race to electrification (though, oddly, it won’t be until 2024 that Aston will start delivering its first hybrid, the Valhalla, and it will have its “core portfolio” fully electric in 2030 (its current portfolio has four vehicles, the DBX, DB11, Vantage, and DBS)), it seems that some companies are focusing on something that isn’t going to provide big returns.
Said another way: Did you ever buy a flashlight because of the batteries?
RELATED CONTENT
-
How Real Is Additive Manufacturing?
There is a lot of discussion about how 3D printing/rapid prototyping/additive manufacturing is revolutionizing manufacturing, including automotive manufacturing.
-
Plastics: The Return of Body Panels?
A problem with plastics and steel structures is a difference in the coefficient of expansion. Some material modifications may ameliorate that problem.
-
3D Printing at Techniplas
Techniplas LLC has been supplying complex plastic components to the auto industry for nearly 100 years.