On Rafael Nadal, BTS, and Carbon Neutrality
A contributor to the VW ID.4 five-star rating? Does that Chevy crate engine look vintage? Can a tennis star and K-pop celebs move the needle on carbon neutrality? Would you buy a car to get a. . .jacket? And developments in the arena of manufacturing process.
This week On Automotive
- A Battery Benefit? VoA’s 2021 ID.4 RWD electric vehicle has achieved a 5-Star overall safety rating
- This Is Not a Throwback: The ZZ632/1000 crate engine
- Geography, Celebrity & Sustainability: Rafael Nadal and the Kia EV6
- Dance, Dance, Dance: Hyundai teams up with BTS
- What Price a Jacket? Lotus offers a high fashion driving jacket
- About the Evija
- What’s this Doing Here? A Machining Center for EV Motors
- Carbon Fiber for Commercial Chassis
//
A Battery Benefit?
Volkswagen of America (VoA) announced last week that its 2021 ID.4 RWD electric vehicle has achieved a 5-Star overall safety rating from the National Highway Traffic Safety Administration (NHTSA).
This means the crossover ran through the New Car Assessment Program (NCAP), which involves frontal and side crash ratings, as well as a rollover resistance test rating.
Which got us to thinking about whether the structural design of the battery electric vehicle has some positive benefits when it comes to collisions.
The ID.4 has an 82-kWh battery pack that consists of 288 pouch cells in 12 modules.
There is an aluminum battery housing that includes both extruded and pressure-cast profiles. This is bolted to the body of the vehicle. It is located so there is a low center of gravity.
The whole thing (including batteries) weighs 1,087 pounds.
Presumably, that helps (a) to provide significant structural rigidity and (b) mitigates the potential of rolling over.
Still, we wondered.
So we asked Matt Renna, VoA Vice President E-Mobility and Innovation.
He answered, good naturedly:
“The battery pack is a giant piece of metal at the center of the car with a zillion fasteners. It most definitely has structural benefit. I think it’s fair to say that the battery pack is a key part of the crash strategy and contributes to the positive ratings from NHTSA and IIHS.”
The ID.4 also received a Top Safety Pick+ rating from IIHS (the Insurance Institute for Highway Safety).
///
This Is Not a Throwback
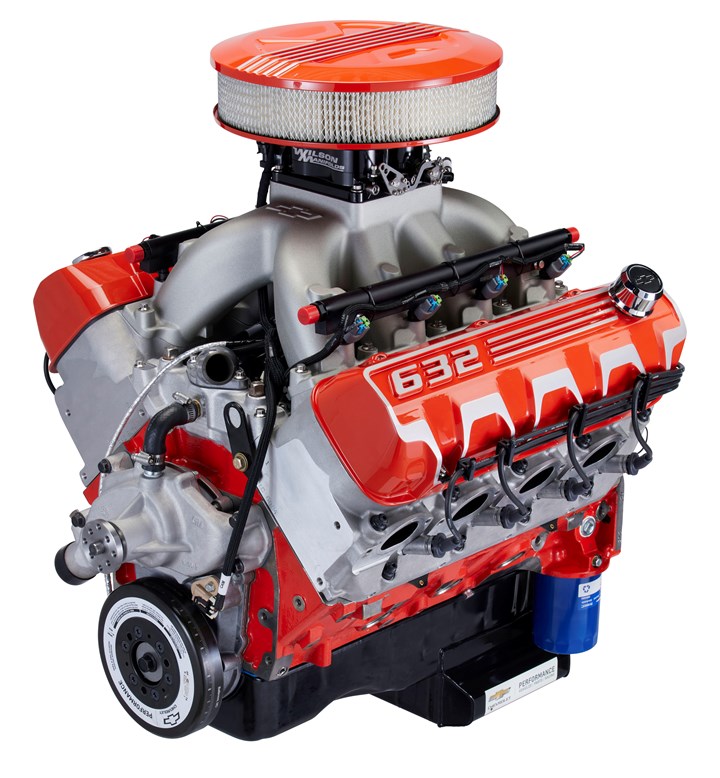
A Big Block crate engine from Chevy: absolutely new. (Image: Chevrolet)
While that engine may look to you like something out of, say, the 1950s, it is brand new. In fact, deliveries won’t start until early 2022.
It is the ZZ632/1000 crate engine from Chevrolet Performance.
Really Big
A “Big Block”—seriously big, as it has a 632-cubic inch displacement—V8 that produces 1,004 hp @ 6,600 rpm and 876 lb-ft of torque @ 5,600 rpm.
The block is, unsurprisingly, cast iron.
The cylinder heads are CNC-machined aluminum.
Apparently, Chevy Big Blocks of the past have had variations in port shape from cylinder to cylinder.
The intake ports of the ZZ632/1000 have the same length, volume and layout. The exhaust ports are identical, too.
The cylinder heads are named “RS-X Symmetrical Port,” named for Ron Sperry, who designed them as one of his last projects in more than 50 years of working on GM performance and racing engines.
(Incidentally, Sperry is responsible for the symmetrical ports on the Gen III LS1 Small Block V8 that first appeared in the 1997 Corvette.)
Russ O’Blenes, GM director of the Performance and Racing Propulsion Team:
“This is the biggest, baddest crate engine we’ve ever built.”
It is being built at the Chevy Performance Race Center in Pontiac, Michigan.
///
Geography, Celebrity & Sustainability

Soon you, too, will be able to drive like Rafael Nadal, in a Kia EV6. (Image: Kia)
Rhode Island is the smallest U.S. state.
It covers 1,214 square miles.
Mallorca is the largest of the Balearic Islands, which are part of Spain.
It covers 1,404 square miles.
This comparative geography lesson is because of an announcement by Kia that Rafael Nadal is going to “increase the use of electric vehicles.”
Kia gave the man, one of the best tennis players on the planet, a customized EV6 GT-Line. The EV6 is Kia’s electric crossover.
It will go on sale in the U.S. early next year.
It certainly isn’t surprising for an OEM to provide a vehicle to a celebrity.
But it is a bit surprising that Nadal is going to use the vehicle on his home island of Mallorca, which we have established is, well, diminutive.
The projected 300-mile range of the EV will undoubtedly be fine on Mallorca. And then some.
When it comes to the U.S., it will handle Rhode Island with ease.
Nadal:
“My job naturally requires a lot of travel, and my lifestyle is not fully sustainable. But I’m determined to make the necessary changes where I can, starting with my personal use of the EV6 crossover in Mallorca and beyond. I feel lucky to have the support of Kia and the new EV6 that will help drive my commitment. I would like to encourage others to join me in driving these kinds of vehicles wherever possible.”
The “and beyond” in that quote is interesting.
There are ferries that run between the Spanish mainland, out of Valencia, and Mallorca.
It takes up to nine hours to make the crossing. Nine hours.
Odds are Nadal won’t be taking the ferry with his EV6.
///
Dance, Dance, Dance
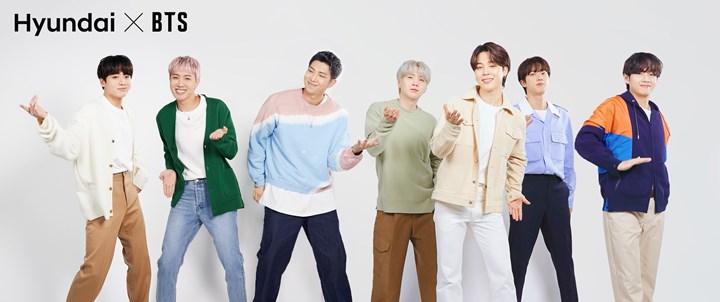
If the biggest pop group in the world is promoting carbon neutrality for Hyundai. . . (Image: Hyundai)
In other celebrity zero-carbon news. . .
Hyundai Motor Company is deploying its “global brand ambassadors,” Korean boy band BTS, to promote carbon neutrality.
This takes the form of two social media challenges, #Move4Gen 1 and #Pass2Gen 1.
The first is a dance challenge. Of course it is.
BTS will demonstrate moves, then the participants will create dances that they’ll post on TikTok, Instagram Reels and YouTube Shorts.
What does that have to do with carbon neutrality? you wonder.
This:
“The choreography features a ‘+’ representing already generated carbon emissions and a‘-’representing reduced carbon emissions that leads to a‘0’ representing net-zero carbon emissions to achieve carbon neutrality.”
Can’t imagine anyone thinking otherwise.
#Pass2Gen 1 involves the participants coming up with things that they want to pass on to Generation One, the generation that will live in a carbon neutral era.
In this case, BTS starts out what is setup as a relay on social media with: “clean water,” “blue sky” and “starlight.”
Hyundai, incidentally, plans to be carbon neutral in both product and process by 2045.
BTW: the average age of BTS members in 2045 will be 50.
///
What Price a Jacket?
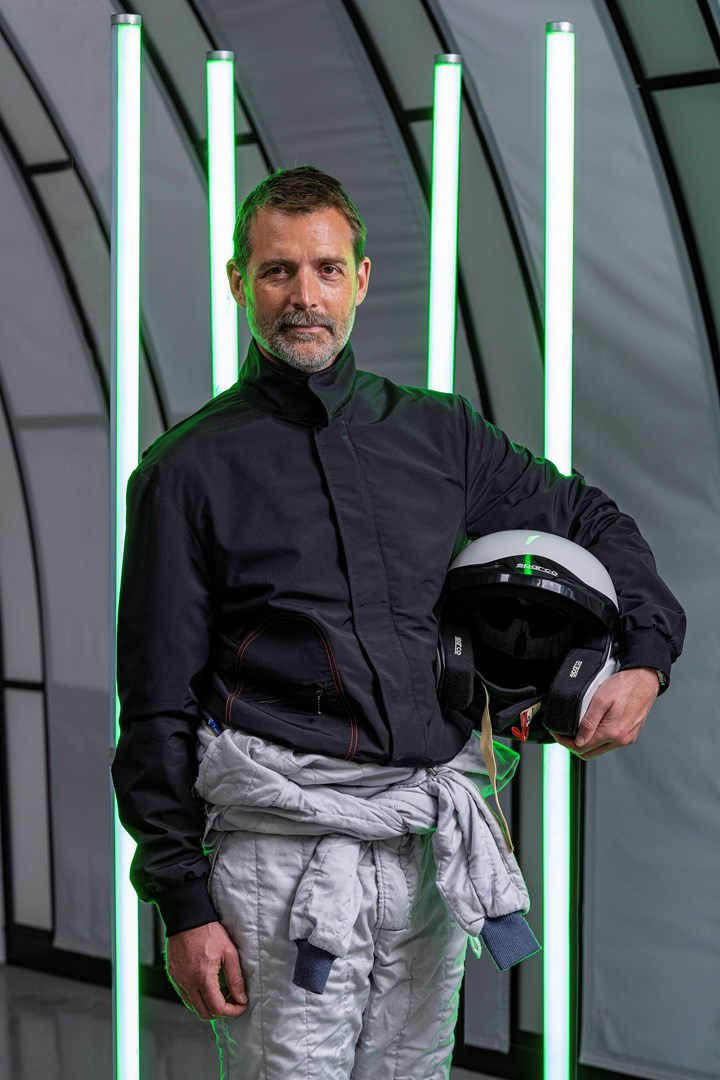
That jacket has quite the pedigree. (Image: Lotus)
In other unusual automotive developments. . .
Lotus Cars, the purveyor of legendary sports cars, is collaborating with Norton & Sons, Saville Row tailors. It has been crafting clothing since 1821.
It could be the definition of the term “authentic.”
The collaboration takes the form of a driving jacket.
The jacket “is made from a superfine lightweight water-resistant merino wool/nylon technical textile manufactured in Italy by Loro Piana, and features state-of-the-art Cobrax and Riri hardware.”
Historic digression
Loro Piana was established in 1924 and Cobrax and Riri in 1936, so they are both much younger than Norton & Sons but older than Lotus Cars.
Colin Chapman, founder of the company, built his first car in 1948. The Mark 3 circuit racing car was built in 1950 and was the first to be called a “Lotus.” In 1951 the Lotus Engineering Company was established. We’d say 1951 is the founding year (as in an actual business being started) but many claim 1948.
At this point you might well be wondering where this is going.
Here:
In order to get this jacket you have to do one thing:
Buy a Lotus Evija, an electric supercar.
It starts at £ 2 million.
Some dealers used to throw in mats.
Lotus is offering a jacket.
///
About the Evija
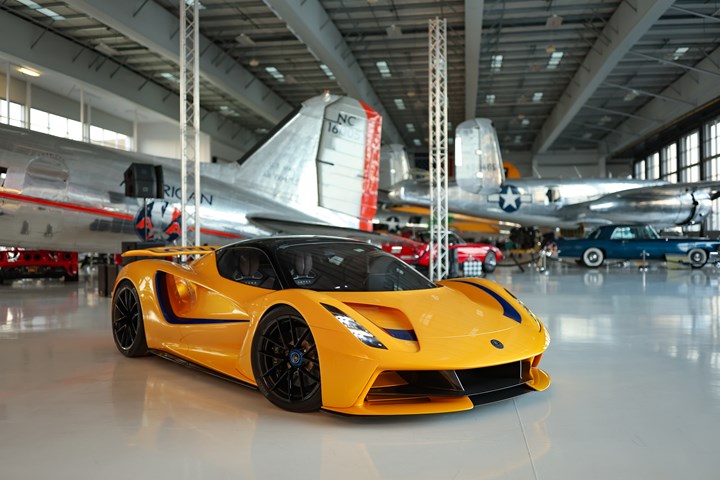
What you can get along with your jacket. (Image: Lotus)
In case you’re wondering about the Evija (“e-vi-ya”), of which 130 will be built. . .
- It has a one-piece carbon fiber monocoque chassis. The weight of the monocoque tub: 239 pounds.
- There are no side view mirrors. Cameras actually pop out of the front quarter panels on either side. There is also a camera on the roof.
- There are four e-motors, with an estimated 493 hp each. The powertrain was developed by Williams Advanced Engineering (WAE). It is well known in the Formula 1 and Formula E racing series.
- WAE also worked on the electrical system. It includes a 2,000-kW lithium-ion battery. It can accept an 800-kW charge, but as one isn’t likely to find one of those, know that it can be charged by a 350-kW unit to 80% in 12 minutes and to 100% in 18 minutes.
- WLPT combined range: 215 miles.
- Top speed: >200 mph.
- The Evija is being built at the Lotus plant in Hethel, where the company has been based since 1966
///
What’s This Doing Here?
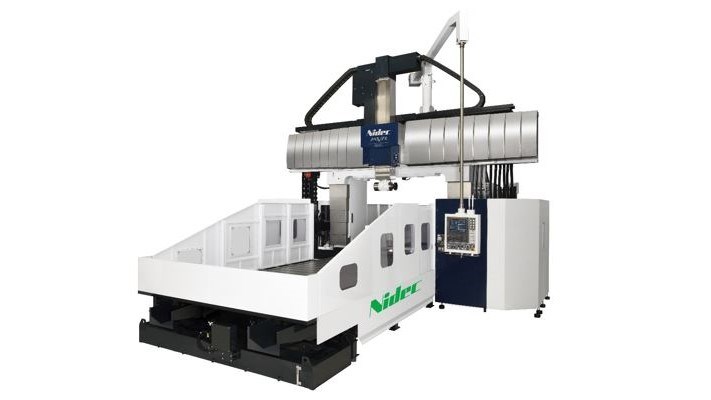
One benefit of this machine is that it can be moved in a 15-ton truck. (Image: Nidec)
Generally we don’t write about machine tools. Not that they aren’t important to the auto industry. They are, in a word, essential.
But as you’ve noticed, there’s a picture of a double-column machining center, the Nidec MVR-Cx, above.
So why is that here?
Two reasons.
- Nidec Corp., which specializes in all types of electric motors, for things ranging from machine tools to computer disc drives to windmills, is putting a big bet on electric vehicles. It aims to produce 10-million EV motors annually by 2030. It is shooting for 40-45% market share in that space. Last year it announced a $1.8-billion investment in three plants to produce EV motors.
- In its description of the machining center it points out the machine“can be carried in a 15-ton truck.” And having read plenty of descriptions of machine tools over the decades, we’ve never seen a benefit based on the mode of transportation.
And for more street cred
A couple weeks back Nidec announced its 200-kW e-axle traction motor system is being used in the Geely Zeekr 001 model.
Worth noting: the Zeekr 001 is based on the Geely Sustainable Experience Architecture (SEA). This platform is also going to be used by Volvo, Lynk & Co. and smart, all Geely marques.
And when SEA was introduced in September 2020, Eric Li, chairman and founder of Geely Holding, said:
“Our development of this transformative electric vehicle architecture marks the biggest leap forward at Geely in more than a decade. This far-reaching innovation will greatly expand the volume and scalability of our zero-emission models, and we intend to offer the benefits of this innovation to other manufacturers – reflecting the common interests in our industry in addressing the challenges of climate change.”
In other words: other OEMs can use the platform, too.
Which undoubtedly will help move even more electric motors.
But machining centers. . . ?
///
Carbon Fiber for Commercial Chassis
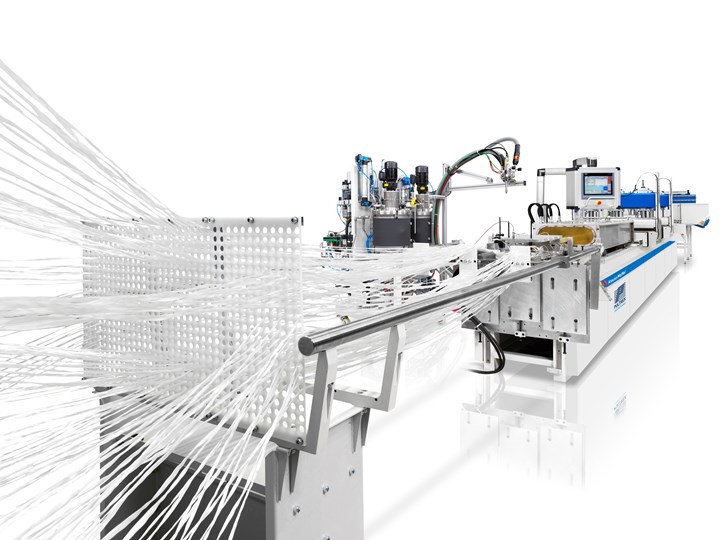
All of those fibers are appropriately oriented and are transformed—with the addition of a polymer matrix—into truck chassis components. (Image: CarbonTT)
One more machine. . .
It is the iPul pultrusion system.
It is used to produce lightweight components from carbon fiber reinforced plastic (CFRP).
The system—developed by Pultrex, a UK-based KraussMaffei subsidiary—is being used by Carbon Truck & Trailer GmbH’s facility in it facility outside of Hamburg to manufacturer components for commercial vehicles.
Reportedly it is one of five of its type in the world.
And Carbon Truck & Trailer made its contribution to the system, developing a roving guide to facilitate the production of wrinkle-free profiles from the multiaxis roving.
The chassis components CarbonTT produces are up to 60% lighter than steel.
Who’s Using It?
We asked Gerret Kalkoffen, Managing Director, Carbon TT.
And he answered that among the customers are/were Mercedes and a company named StreetScooter. . .which doesn’t make scooters, but commercial delivery trucks (as it is a subsidiary of Deutsche Post DHL Group).
Presently, said Kalkoffen, “The Mercedes-Benz Carbon Sprinter has undergone dynamic testing and is going into its durability testing in Q1/2022. We hope to go to market in Q2/Q3 2022.”
The StreetScooter deployment was on the Work L truck for the German postal system and a commercial application, but Kalkoffen noted, “Due to corporate restructuring and decisions beyond our control, the further deployment was stopped.”
Of the applications, he said, “Both the Work L as well as the Sprinter are based on a design with pultruded CFRP profiles, which allows a very cost effective, large-scale and high-quality production. We developed a process that lets us optimize the fiber orientation despite high automation. We hold various IP in the design of CFRP parts, the production process and interface and bonding technologies.”
When the name of your company is “Carbon Truck & Trailer,” clearly the commitment to CFRP is certainly fundamental.
RELATED CONTENT
-
Engineering the 2019 Jeep Cherokee
The Jeep Cherokee, which was launched in its current manifestation as a model year 2014 vehicle, and which has just undergone a major refresh for MY 2019, is nothing if not a solid success.
-
Jeeps Modified for Moab
On Easter morning in Moab, Utah, when the population of that exceedingly-hard-to-get-to town in one of the most beautiful settings on Earth has more than doubled, some people won’t be hunting for Easter eggs, but will be trying to get a good look at one of the vehicles six that Jeep has prepared for real-life, fast-feedback from the assembled at the annual Easter Jeep Safari.
-
On Fuel Cells, Battery Enclosures, and Lucid Air
A skateboard for fuel cells, building a better battery enclosure, what ADAS does, a big engine for boats, the curious case of lean production, what drivers think, and why Lucid is remarkable